Immediate detection of damage in fiber composite materials
Research group develops detection method
In the ISAFAN research project, scientists at TH Köln are developing an improved method for detection and prediction of damage in fiber composites. A new technology, which is applied for a patent, could in the future precisely detect damage, such as fiber breaks, and cut down on expensive maintenance work.
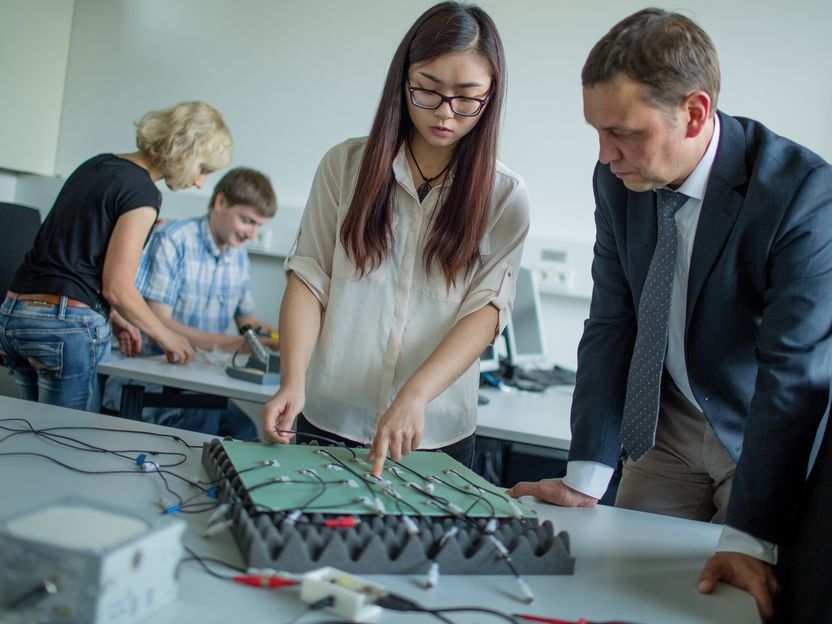
Thilo Schmülgen/TH Köln
To detect damage, the ISAFAN research group (German abbreviation for Intelligent Damage Prediction in Fiber Composite Material Components in Industrial Applications) at the Gummersbach campus of TH Köln – University od Applied Sciences has developed a diode matrix that can be integrated in composite components. "We apply electrical current to the conducting paths of the matrix in series". Project spokesman Professor Jochen Blaurock explains the invention: "If there is damage, the conducting paths are interrupted, and the system registers the change in electrical properties".
Currently, workpieces of fiber composite are often subjected to extensive ultrasonic testing during maintenance, in order to detect damage. The new technology makes it possible to detect problems at the moment they occur and to initiate suitable measures. Since the conducting paths are clocked in the range of milliseconds, the component is completely monitored at all times. Furthermore, the location is all the more precise, the tighter the matrix grid. The technology is suitable for fiber composite parts of all shapes. Currently the research group is searching for a suitable material for the diode matrix. "In addition to conductivity, it is especially important that the material have an elongation at break similar to that of the material in which it is contained. That means that the fiber composite and the conducting paths should have similar mechanical properties. Because, if one of the two fails sooner than the other, the damage cannot be measured exactly", explains Blaurock.
To make it possible to use the new technology in industrial mass production, the team is now developing a method for efficient integration of the diode matrix into the components. "Ideally the wire matrix would be applied to a foil which is implemented in the component during the production process. We are still searching for an industrial partner for this purpose", says Blaurock.
Product life cycle
In addition to the detection of direct damage, the research group is also working to prognosticate material fatigue and residual service life. In this context the component is stimulated with a sound wave, and the system response, meaning the reaction of the component, is measured. If the properties of the component change, for example due to fatigue or damage, the system response changes. Using statistical and physical models, the service life can be prognosticated. In addition, operators of wind power systems, for example, can detect problems in blade materials as they develop and take them into consideration when planning maintenance intervals.
With support from PROvendis GmbH, the patent marketing company of the universities in NRW, TH Köln has filed a patent for the invention of Prof. Michael Bongards and Hartmut Köhn.
Other news from the department science
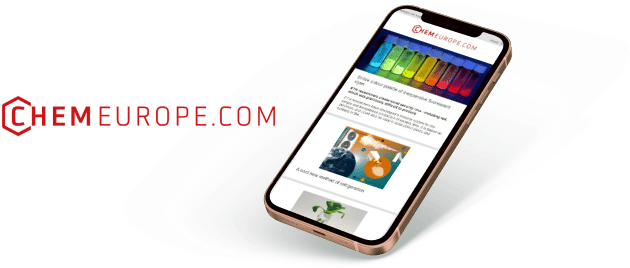
Get the chemical industry in your inbox
By submitting this form you agree that LUMITOS AG will send you the newsletter(s) selected above by email. Your data will not be passed on to third parties. Your data will be stored and processed in accordance with our data protection regulations. LUMITOS may contact you by email for the purpose of advertising or market and opinion surveys. You can revoke your consent at any time without giving reasons to LUMITOS AG, Ernst-Augustin-Str. 2, 12489 Berlin, Germany or by e-mail at revoke@lumitos.com with effect for the future. In addition, each email contains a link to unsubscribe from the corresponding newsletter.