New CMI process recycles valuable rare earth metals from old electronics
Scientists at the Critical Materials Institute have developed a two-step recovery process that makes recycling rare-earth metals easier and more cost-effective. Rare-earth metals are valuable ingredients in a variety of modern technologies and are found in cell phones, hard disk drives in computers, and other consumer electronics, which are frequently discarded for newer and more up-to-date versions.
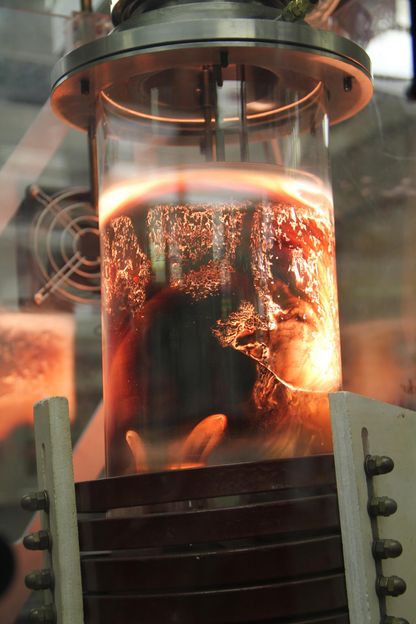
According to the Environmental Protection Agency, U.S. consumers disposed of 3.4 million tons of electronics waste in 2012. Continuously increasing global demand for new consumer electronics in turn drives demand for rare-earth metals, which are difficult and costly to mine. But recycling rare earths isn't necessarily any easier.
"Recycling rare-earth metals out of consumer waste is problematic, and there are multiple obstacles in the entire chain from manufacturing to collection infrastructure to sorting and processing," said CMI scientist Ryan Ott. "We're looking at ways to make the processing part of that chain - removing the rare-earths from scrap magnet material - better."
Building upon previous research work done at the Ames Laboratory, Ott and his research group have developed a two-stage liquid metal extraction process that uses differences between the solubility properties of different elements to separate out rare-earth metals.
"Magnesium has good solubility with rare-earths, particularly with neodymium, and poor solubility with the other components of magnets, like iron and boron," said Ott.
In the liquid extraction method CMI has developed, scrap metals are melted with magnesium. The lighter atomic weight rare earths like neodymium bind with the magnesium and leave the iron scrap and other materials behind. Then the rare earths are recovered from the magnesium through vacuum distillation.
In the second step, another material is used to bind with and extract the heavier atomic weight rare earths, like dysprosium.
Finding the best way to do the second step was the important breakthrough, Ott said.
"Extraction of the heavier rare earths was always the difficulty of this process, and those materials are the most valuable. So finding a way to do that successfully was the key to making it more economically viable as a large-scale recycling method."
Other news from the department science
Most read news
More news from our other portals
See the theme worlds for related content
Topic world Extraction
Extraction is a fundamental process in the chemical laboratory that enables specific components to be isolated and concentrated from a mixture. Whether it's extracting active ingredients from natural products, removing impurities from synthesis products, or preparing analytical samples, extraction is a key step in achieving precise and efficient results in chemical research and analysis.
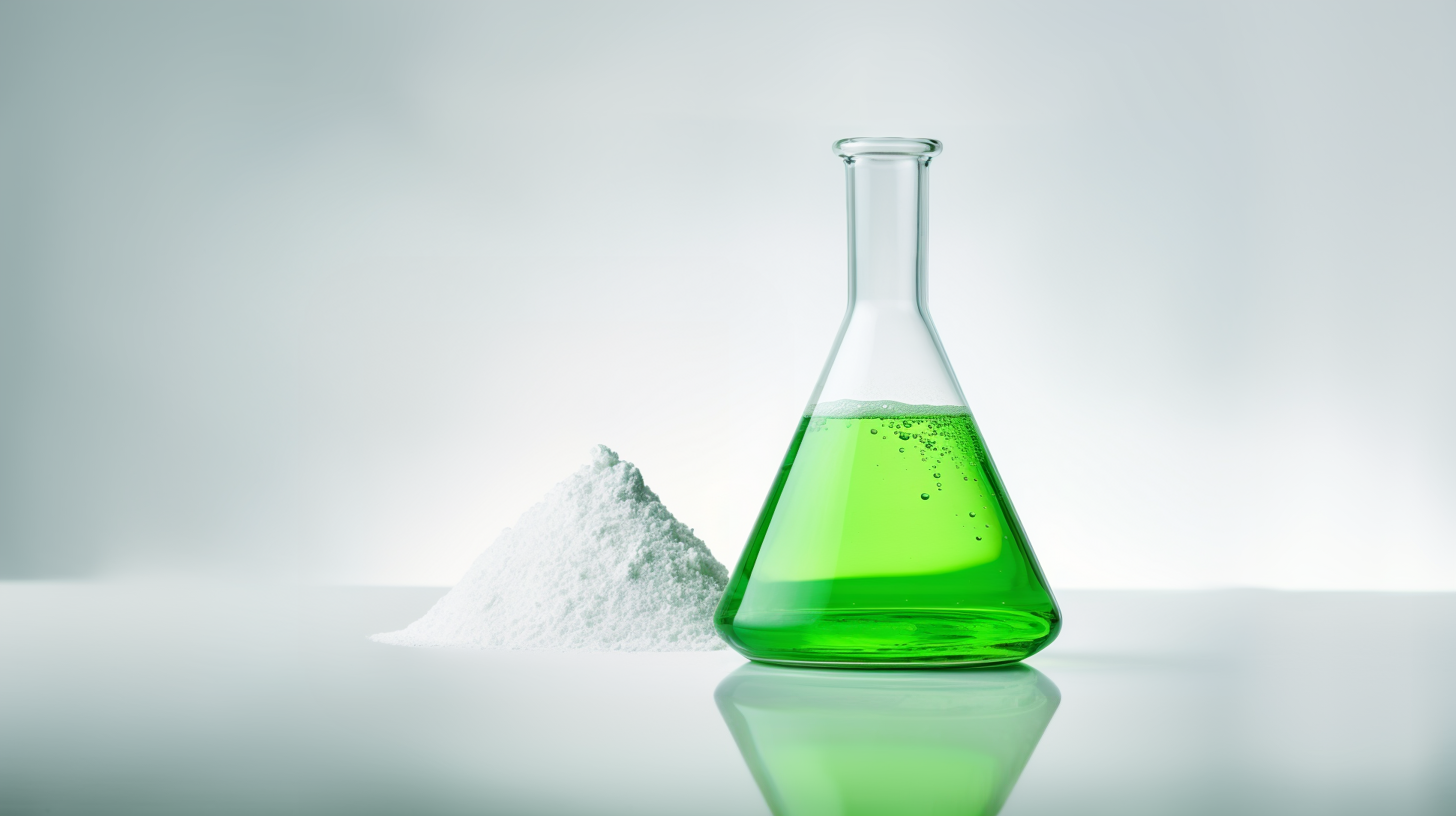
Topic world Extraction
Extraction is a fundamental process in the chemical laboratory that enables specific components to be isolated and concentrated from a mixture. Whether it's extracting active ingredients from natural products, removing impurities from synthesis products, or preparing analytical samples, extraction is a key step in achieving precise and efficient results in chemical research and analysis.