De l'engrais à la source d'énergie du futur
Ammoniac : de belles perspectives
Annonces
L'Ammoniac est traditionnellement utilisé pour la production d'engrais. À l'avenir, il pourrait également jouer un rôle clé dans la transition énergétique en tant que source efficace d'hydrogène et substitut respectueux du climat aux combustibles fossiles, puisqu'il peut être produit à partir d'azote et d'hydrogène sans aucune émission de carbone. En outre, l'ammoniac présente de nombreux avantages en termes de transport et de stockage. L'Institut Fraunhofer pour la microtechnique et les microsystèmes IMM travaille sur une technologie de craquage de l'ammoniac peu encombrante, efficace et surtout décentralisée dans le cadre de nombreux projets de recherche.
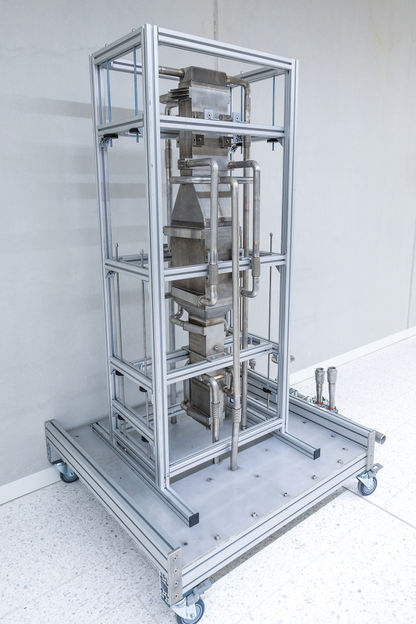
Installation pilote Fraunhofer IMM pour le craquage de l'ammoniac avec une capacité de craquage de 20 kg/h
© Fraunhofer IMM
"L'ammoniac offre de très bonnes perspectives pour la transformation durable de notre système énergétique", explique Gunther Kolb, chef de la division Énergie et directeur adjoint de l'institut Fraunhofer IMM à Mayence. "Après tout, produire suffisamment d'énergie sans émissions n'est pas le seul défi de la transition énergétique. Étant donné que de grandes quantités d'électricité verte peuvent être produites principalement dans des endroits où il y a beaucoup de vent ou de soleil, comme au Chili et en Australie, le transport à faible perte vers des zones où il y a moins d'énergie renouvelable disponible est en effet un facteur important." L'utilisation de l'ammoniac peut apporter des avantages transformateurs à cet égard.
Parfaitement adapté au stockage et au transport de l'hydrogène
L'hydrogène vert (H2) se combine à l'azote (N2) dans un rapport de 3:1 pour produire de l'ammoniac (NH3) et l'énergie stockée et transportée sous cette forme (c'est-à-dire l'ammoniac) subit moins de pertes dans la chaîne d'approvisionnement. En outre, l'ammoniac présente quelques avantages par rapport à l'hydrogène pour le stockage de l'électricité. Il reste liquide à la pression atmosphérique et même à une pression de seulement 7,5 bars ou lorsqu'il refroidit à seulement -33°C environ. En revanche, pour liquéfier l'hydrogène pur, il faut l'introduire dans un vide à basse pression et abaisser la température à -253°C, ce qui nécessite beaucoup d'énergie. En outre, la densité énergétique volumétrique de l'ammoniac est plus élevée que celle de l'hydrogène liquide, de sorte qu'il peut transporter plus d'énergie par unité de volume. "La production d'ammoniac à partir d'hydrogène et d'azote ne nécessite qu'environ 5 % d'énergie en plus que la production d'hydrogène à partir d'électricité verte", explique M. Kolb. "De plus, la production et le craquage de l'ammoniac sont presque totalement exempts de carbone. L'ammoniac est toxique et inflammable, il est donc classé comme dangereux et soumis à des réglementations strictes. Grâce aux normes de sécurité élevées en vigueur, quelque 25 millions de tonnes d'ammoniac sont actuellement transportées en toute sécurité dans le monde entier par bateau et par train chaque année, principalement pour la production d'engrais.
Réseau principal d'hydrogène en cours de développement
L'ammoniac doit être reconverti en ses composés d'origine (azote et hydrogène) pour être utilisé dans l'industrie chimique ou comme source d'énergie. Il est tout aussi important que cela se fasse avec un minimum de pertes d'énergie. L'ammoniac sous forme de gaz est introduit dans un réacteur à une température d'environ 600 degrés Celsius, où il entre en contact avec un catalyseur inorganique à base de nickel doté d'une grande surface interne. "Actuellement, les premières grandes installations d'électrolyse sont construites dans des pays riches en électricité verte, comme l'Australie et le Chili, pour produire de l'ammoniac. En Europe, l'une des premières grandes installations de craquage est en cours de construction à Rotterdam, par exemple", précise M. Kolb. L'objectif est de fournir de l'hydrogène là où il est nécessaire par le biais de pipelines. Le principal problème est que de nombreux clients potentiels, en particulier les PME, n'ont pas accès aux pipelines d'hydrogène. L'infrastructure allemande de l'hydrogène est actuellement en cours de construction. Les plans prévoient la mise en place, d'ici à 2032, d'un réseau central d'hydrogène comprenant environ 9 000 kilomètres de canalisations au total, principalement en convertissant des conduites de gaz naturel. Cependant, même après cela, de vastes zones ne seront pas connectées à l'approvisionnement en hydrogène.
Approvisionnement local grâce à une technologie de craquage décentralisée
"Notre technologie de craquage décentralisé peut combler ce manque d'approvisionnement de manière efficace et sans émissions pour des quantités d'hydrogène requises comprises entre 100 kilogrammes et 10 tonnes métriques par jour", explique M. Kolb. "Dans le cadre du projet AMMONPAKTOR, financé par le Land de Rhénanie-Palatinat, nous nous sommes associés à l'Institut Fraunhofer de mathématiques industrielles ITWM pour mettre au point un craqueur d'ammoniac compact qui atteint un rendement de 90 % au cours du processus de reconversion grâce à notre technologie innovante d'échangeur de chaleur à plaques et à la combustion intégrée des gaz d'échappement provenant de l'adsorption à variation de pression utilisée pour le nettoyage, contre 70 % pour les technologies conventionnelles."
L'énergie nécessaire pour chauffer le réacteur est générée directement dans le réacteur de craquage à l'aide des flux de gaz d'échappement, de sorte qu'aucun combustible ou électricité supplémentaire n'est nécessaire pour le craquage. Le réacteur AMMONPAKTOR est également 90 % plus petit que la technologie conventionnelle. Ceci est particulièrement important pour les applications mobiles et à espace restreint. L'utilisation des gaz d'échappement signifie également que la technologie a une empreinte carbone plus faible que les concepts de réacteurs chauffés à l'électricité. "Outre l'utilisation interne des gaz d'échappement du système, l'échangeur de chaleur à plaques innovant de Fraunhofer IMM, qui est directement recouvert d'un catalyseur, fait toute la différence", explique M. Kolb. "Au lieu de la méthode conventionnelle consistant à générer la chaleur nécessaire au craquage dans un système de tuyaux chauffés de l'extérieur à environ 900 degrés Celsius, ce qui nécessite beaucoup d'énergie, notre technologie génère la chaleur à l'endroit même où elle est nécessaire, ce qui permet à notre système d'avoir un bien meilleur transfert de chaleur. Cela se traduit par d'énormes économies d'énergie".
Un prototype achevé sur le site de Fraunhofer IMM à Mayence permet déjà de produire environ 75 kg d'hydrogène par jour, soit à peu près la production journalière d'une pile à combustible de 50 kilowatts. "Ce volume suffirait à lui seul à alimenter une petite station-service d'hydrogène, par exemple", note M. Kolb. Pour l'instant, le prochain objectif de développement est de passer à une production quotidienne de 10 tonnes, notamment dans le cadre du projet maritime quinquennal de l'UE GAMMA et du projet phare Fraunhofer AmmonVektor, qui explore l'ensemble de la chaîne de valeur de l'ammoniac vert afin de rendre l'hydrogène disponible de manière décentralisée et à un coût aussi bas que possible. Ce projet triennal, dirigé par l'Institut Fraunhofer pour les technologies de l'environnement, de la sécurité et de l'énergie UMSICHT, est en cours depuis le début de l'année 2024.
Note: Cet article a été traduit à l'aide d'un système informatique sans intervention humaine. LUMITOS propose ces traductions automatiques pour présenter un plus large éventail d'actualités. Comme cet article a été traduit avec traduction automatique, il est possible qu'il contienne des erreurs de vocabulaire, de syntaxe ou de grammaire. L'article original dans Anglais peut être trouvé ici.