Braskem inaugurates two plants in Bahia
The two new plants at the Camaçari Industrial Complex for manufacturing ETBE - a bioadditive produced from renewable raw materials - received investments of R$100 million
Braskem inaugurates two new plants at the Camaçari Industrial Complex. They represent a new landmark in the company’s operations in the world of renewable materials. The plants will produce ETBE, a bioadditive for gasoline made from renewable raw material. The installation project for the new units absorbed investments of around R$ 100 million, with a total annual production capacity of 212 thousand tons of the product.
"Like the Green Plastic, which will begin to be produced on an industrial scale starting next year at the Triunfo Complex, in Rio Grande do Sul, ETBE is an innovation that stems from research Braskem has been carrying out over the past three years, when the company faced the challenge to find a sustainable alternative to replace MTBE, as a result of the environmental restrictions the product was encountering in the international market, mainly from the Japanese and American markets," says Manoel Carnaúba, vice-president of Basic Petrochemicals at Braskem.
With the specification of ETBE, Braskem begins to set aside part of production for the Japanese market as a result of the long-term contract signed with Sojitz Corporation. The agreement involves the supply of 120 thousand tons of the product over three years. In Japan, the introduction of fuels derived from biomass was decided in the Kyoto Protocol. Beginning in 2010, the Japanese oil industry plans on placing 840,000 m³ of ETBE per year. Approximately four million tons of ETBE per year are already being sold to Europe. Sojitz will begin to sell ETBE starting in 2009 and its goal is to expand these volumes in order to serve the Japanese and European markets.
Investments in Bahia
By the end of 2009, Braskem will invest about R$ 200 million in Bahia, besides the R$ 100 million invested in the two new plants. Of that sum, R$ 50 million are being used to modernize and expand the factory’s PVC production capacity, and R$ 22 million have already been invested in the construction of the Santa Helena Pipeline, in partnership with Embasa. The rest will be used to modernize and upgrade technology at the company's production units in Bahia.
Innovation and Sustainability
The ETBE plants in Bahia have what is most modern at Braskem in terms of safety - whether process safety (industrial reliability) or occupational safety for people ETBE (Ethyl Tertiary-butyl Ether) is obtained from ethanol’s (43%) reaction to isobutene (57%), which characterizes it as a bioadditive. Since it is generated using renewable raw material (ethanol) ETBE makes it possible to capture CO2 emissions. "For every ton of ETBE produced, we stop emitting 783 kilograms of carbon in the upstream chain (impact prior to consumption)," says Mário Pino, manager of Corporate SSMA at Braskem, underscoring that this emission reduction demonstrates in practice the company’s orientation towards sustainability.
ETBE’s specification in Bahia, which occurred in July, was very significant for Unib - the Basic Petrochemicals Unit, because besides the sustainability attributes that involve the product, project installation took place wit-out any safety or environmental occurrence. According to Murilo Amorim, manager of Aromatic Production, the result "was a true example of entrepreneurship by all those involved, which represents the undertaking’s success, from conception to assembly and start-up of the plant."
According to Pitiguara Moreira, Coordinator of Undertakings and responsible for project installation, "ETBE’s challenge was an important event at Unib-BA in several aspects, involving teams from different areas. "We had to invest a lot in project planning and execution because ETBE is a product that is part of a production chain. With the premise of interrupting the production chain for as short a time as possible, it was necessary to have great alignment between areas, so we could take advantage of every opportunity to prepare the units for final project implementation," says Pitiguara.
Other news from the department manufacturing
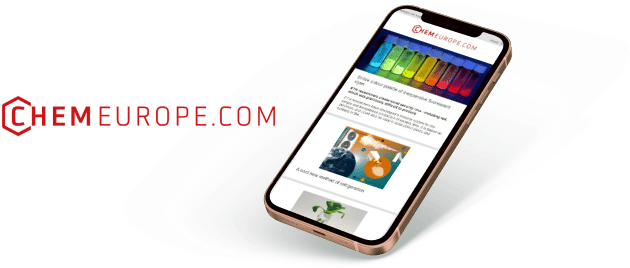
Get the chemical industry in your inbox
By submitting this form you agree that LUMITOS AG will send you the newsletter(s) selected above by email. Your data will not be passed on to third parties. Your data will be stored and processed in accordance with our data protection regulations. LUMITOS may contact you by email for the purpose of advertising or market and opinion surveys. You can revoke your consent at any time without giving reasons to LUMITOS AG, Ernst-Augustin-Str. 2, 12489 Berlin, Germany or by e-mail at revoke@lumitos.com with effect for the future. In addition, each email contains a link to unsubscribe from the corresponding newsletter.