Air Products Polymers' Newest Product Offers Formulators Improved Performance and Environmental Benefits
LEHIGH VALLEY, Pa., Aug. 7 - The performance advantages of vinyl acetate-ethylene (VAE) emulsions for use in architectural paint formulations have long been recognized in the coatings industry. The cost of VAEs versus vinyl acrylics has inhibited broad adoption of this technology in the market. Air Products Polymers, L.P., the recognized world leader in VAE emulsions, has solved that problem with its new Airflex(R) EF811 emulsion product offering.
Developed as a high-performance, cost-competitive replacement for vinyl acrylic copolymers, Airflex EF811 emulsion polymer is an aqueous dispersion of a VAE copolymer. "This product is a major breakthrough for the coatings industry," said Heidi Alderman, business manager, Coatings for Air Products Polymers. "It has all the performance attributes the industry looks for in a VAE, is priced comparably to vinyl acrylics, and allows paint formulators to meet stringent VOC (volatile organic compound) standards through its significantly lower solvent demand than vinyl acrylics."
Formulators can rely on Airflex EF811 emulsion, in interior or exterior applications, for superior scrub resistance, excellent low temperature touch- up, and low VOC formulating. "There are no specific raw materials that are needed to formulate high quality architectural coatings with this product," said Andy DeFusco, senior applications chemist at Air Products Polymers. "We've studied its performance on our state-of-the-art test fence (in Allentown, Pa.) as both the sole binder and in blends with acrylics. After over a year of exposure, Airflex EF811 VAE emulsion has similar exterior performance to vinyl acrylics, with the exception of masonry coatings. In this case, Airflex EF811 emulsion has significantly better alkaline hydrolysis resistance than vinyl acrylics."
An area where Airflex EF811 emulsion truly shines is scrub resistance for architectural coatings. In all of the formulations tested, Airflex EF811 emulsion significantly out-scrubbed both conventional high scrub vinyl acrylics, as well as newer, low VOC vinyl acrylics. "It sets a new standard," said DeFusco. "Airflex EF811 emulsion has the highest level of scrub resistance of any other commercial emulsion binder in the industry. This includes other VAEs that have previously been recognized as industry standards, like our own Airflex(R) 809 emulsion."
Use of Airflex EF811 emulsion also provides the solution to low temperature touch-up issues, a noted concern of many contractors. "This product exhibits excellent ambient and low temperature touch-up properties in contractor flat paints, even at low VOC levels," said DeFusco.
Additionally, Airflex EF811 emulsion provides formulators with an answer to ever-tightening environmental restrictions on the permissible level of VOCs in coatings. These restrictions require using lower solvent levels in formulating and create performance issues for conventional vinyl acrylics. Airflex EF811 emulsion requires only a minimal amount of coalescing solvent and allows paint formulators to meet newer VOC requirements easily, without impacting performance.
Most read news
Topics
Organizations
Other news from the department research and development
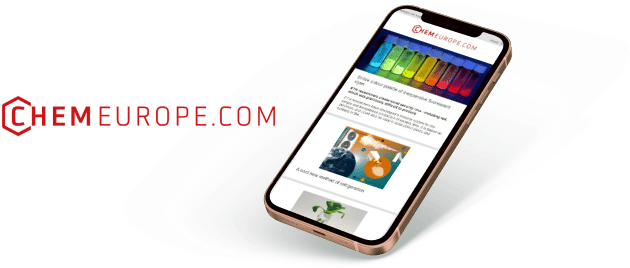
Get the chemical industry in your inbox
From now on, don't miss a thing: Our newsletter for the chemical industry, analytics, lab technology and process engineering brings you up to date every Tuesday and Thursday. The latest industry news, product highlights and innovations - compact and easy to understand in your inbox. Researched by us so you don't have to.