Bayer and DuPont expand leading position in engineering thermoplastics
Dedication of world-scale plant for the production of polybutylene terephthalate (PBT)
Advertisement
With the dedication of a world-scale plant for the production of polybutylene terephthalate (PBT) in Hamm-Uentrop, Germany, Bayer and DuPont are building on their position as leading manufacturers of engineering thermoplastics. With an initial capacity of 80,000 tons per year, the plant is the biggest of its kind in the world. It will be operated by DuBay Polymer GmbH, a joint venture between Bayer and DuPont. The two companies have together invested some 50 million euros in the plant, in which 61 people are employed. For a company to thrive in today's highly competitive market, it must be able to supply top-quality PBT at competitive prices. In Europe, this is only possible with large world-scale plants and state-of-the-art production technology. "Neither of the two companies, DuPont or Bayer, can make adequate use of such a plant immediately on their own, despite the favorable growth forecasts," said Dr. Hagen Noerenberg, head of Bayer Polymers, at the dedication ceremony. "With the jointly operated facility, both partners will strengthen their positions in the keenly contested global market for PBT," said Ferdinand Bauerdick, DuPont´s Director Europe Engineering Polymers, who is also responsible for the global polyester business of DuPont. Both companies use the straight resin from the production facility and compound it into products for their PBT ranges - Crastin® in the case of DuPont, and Pocan® in Bayer's case.
In 2002, some 140,000 tons of the polymer were processed in Europe. Global demand for PBT will grow in the next few years at an above-average rate of somewhere between six and eight percent a year.
The new production plant at DuPont's Hamm-Uentrop site is integrated entirely into the infrastructure of the Chemical Park - from the energy supply to the traffic links and raw material logistics. The new PBT plant, which was built in just under two years, also sets new standards in terms of environmental protection and occupational safety. For example, no solvents are used to manufacture the plastic, and the only by-product, methanol, is fed back completely into the production process. "Virtually 100 percent of the raw materials go into the desired product. In this way, we conserve valuable resources," said Dr. Hubert Fink, chairman of the members committee of DuBay Polymer GmbH.
Most read news
Other news from the department business & finance
These products might interest you
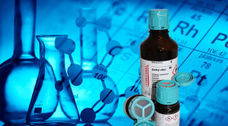
ERBAdry by CARLO ERBA Reagents
Anhydrous solvents from CARLO ERBA Reagents in a clever redesign
ERBAdry series impresses with the latest generation of septa and sealing caps
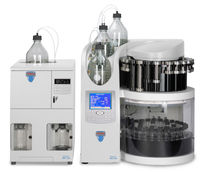
Thermo Scientific™ Dionex™ ASE™ 150 or 350 Accelerated Solvent Extractor systems by Thermo Fisher Scientific
Accelerated Solvent Extraction (ASE) – Maximize results and reduce errors in food analysis!
More extractions in less time using less solvent
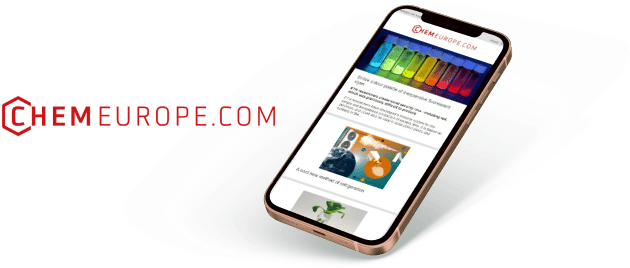
Get the chemical industry in your inbox
By submitting this form you agree that LUMITOS AG will send you the newsletter(s) selected above by email. Your data will not be passed on to third parties. Your data will be stored and processed in accordance with our data protection regulations. LUMITOS may contact you by email for the purpose of advertising or market and opinion surveys. You can revoke your consent at any time without giving reasons to LUMITOS AG, Ernst-Augustin-Str. 2, 12489 Berlin, Germany or by e-mail at revoke@lumitos.com with effect for the future. In addition, each email contains a link to unsubscribe from the corresponding newsletter.