A quantum leap in the manufacture of chlorine from hydrochloric acid
Change in technology brings considerable energy savings
In the manufacture of chlorine from hydrochloric acid Bayer is exploring new avenues. A process of electrolysis based on the oxygen Depolarised Cathode (ODC) technology developed by Bayer and a number of partners requires some 30 percent less electricity than the diaphragm process which has previously been the norm at Bayer. A hydrochloric acid electrolysis unit operating according to the new process has been started up at the Brunsbüttel site. Once the second start-up stage has been completed, annual capacity will rise to 20,000 metric tons of chlorine per year. Chlorine is an important basic chemical and essential for the manufacture of many product lines of Bayer, including polyurethanes and polycarbonate, the latter supplied under the well known tradename Makrolon®. The conversion of chlorine with organic hydrocarbons often results in the generation of hydrochloric acid as a byproduct. This hydrochloric acid can be converted back into chlorine with the aid of electric current. Conventional hydrochloric acid electrolysis generates not only chlorine, but hydrogen as well. The secret of the ODC process is that it suppresses the generation of hydrogen. "In principle we have incorporated a fuel cell process," says Dr. Fritz Gestermann, who is responsible at Bayer MaterialScience AG for process development in the field of electrolysis." With the aid of a so-called Oxygen Depolarised Cathode, oxygen gas can be fed into the process. In this way water forms on the cathode instead of hydrogen." As a result, the electrolysis can be operated at a significantly reduced voltage at the same current density, which leads to less energy consumption.
This has significant advantages including significantly reduced costs and fewer carbon dioxide emissions from energy generation. The OCD process supplies pure chlorine which can be recycled directly without the need for cleaning steps in between, and the amount of chlorine produced can be much more flexibly adjusted to the actual requirement. Even after brief standstills the unit, in stand-by mode, can start supplying chlorine of high quality again at short notice.
The new unit at Brunsbüttel was developed and brought to industrial maturity through a program of cooperation between Bayer AG, UHDENORA, a joint venture between UHDE, Dortmund, Germany, and De Nora, Milan, Italy, and De Nora North America. In the new process a purely metallic electrolysis cell with an ion exchanger membrane is being used in hydrochloric acid electrolysis for the first time. It is planned to license and subsequently market the new technology.
Most read news
Topics
Organizations
Other news from the department business & finance
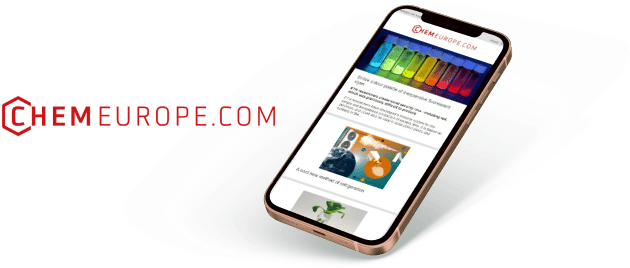
Get the chemical industry in your inbox
By submitting this form you agree that LUMITOS AG will send you the newsletter(s) selected above by email. Your data will not be passed on to third parties. Your data will be stored and processed in accordance with our data protection regulations. LUMITOS may contact you by email for the purpose of advertising or market and opinion surveys. You can revoke your consent at any time without giving reasons to LUMITOS AG, Ernst-Augustin-Str. 2, 12489 Berlin, Germany or by e-mail at revoke@lumitos.com with effect for the future. In addition, each email contains a link to unsubscribe from the corresponding newsletter.