BASF's Freeport Facility Wins National Energy Efficiency Award
BASF's Freeport site has been recognized by the American Chemistry Council (ACC) as a winner of the organization's 2003 "Energy Efficiency Award."
BASF has now won the award 11 times, and, with this award, was one of only five companies to receive the ACC's prestigious "Exceptional Merit" designation.
During a three-month period in 2003, BASF's Freeport Site Energy Team implemented a number of practices and procedures that resulted in a savings of $2.8 million in energy costs and an annual net carbon dioxide emissions reduction of approximately 2,700 tons.
"The ACC congratulates BASF on its accomplishment. These awards publicly recognize that energy efficiency projects not only reduce greenhouse gases and other emissions but also add appreciably to each company's bottom line," said Charles Van Vlack, Executive Vice President of the ACC. "It's a win-win situation for the country, because the improvements protect the environment while helping American business compete globally."
"As the world's leading chemical company, BASF is committed not only to making products better but also to the values and principles of Sustainable Development," said Art Colwell, Vice President and General Manager of BASF's Freeport site. "Thanks to the innovative thinking and teamwork of the BASF team, we are delivering substantive results in support of environmental excellence."
Specifically, the actions BASF took that resulted in the savings and reductions included improving waste burning practices, "mothballing" a partially loaded thermal oxidizer and shifting its load to another partially loaded unit, changing minimum "fire set-points" on two steam generators, and various tuning, operational and maintenance improvements.
"A lot of the credit for this award is owed to BASF's overall energy management structure," said Thomas Theising, BASF's Manager of Energy Systems and Energy Audit Team Leader in Freeport. "Our energy auditing process is a modified version of conventional energy auditing which results in 'deep- seating' energy conservation and energy awareness into the manufacturing site's culture. BASF method goes beyond the conventional, with in-depth involvement of production personnel and a 'question everything' design of reviewing current practices. We also try to have as diverse a cross section of the facility as we can get, from operations, to maintenance, to purchasing, to accounting, to engineering. The result is better approaches and solutions because of the collective intelligence of the group."
Most read news
Other news from the department manufacturing
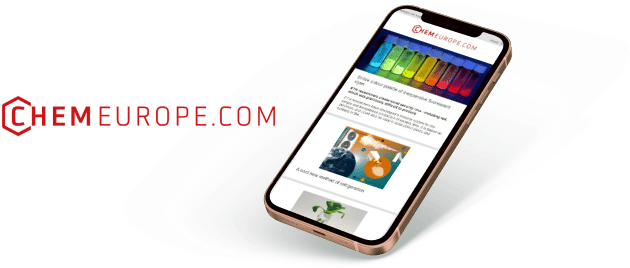
Get the chemical industry in your inbox
By submitting this form you agree that LUMITOS AG will send you the newsletter(s) selected above by email. Your data will not be passed on to third parties. Your data will be stored and processed in accordance with our data protection regulations. LUMITOS may contact you by email for the purpose of advertising or market and opinion surveys. You can revoke your consent at any time without giving reasons to LUMITOS AG, Ernst-Augustin-Str. 2, 12489 Berlin, Germany or by e-mail at revoke@lumitos.com with effect for the future. In addition, each email contains a link to unsubscribe from the corresponding newsletter.