Fraunhofer FEP introduces arcPECVD: A novel roll-to-roll PECVD process
Layers can be deposited in a highly productive way at a coating rate of more than 2000 nm ∙ m/min with the newly developed arcPECVD process. Potential fields of application are layer systems with optical functionalities or permeation barriers on polymer films.
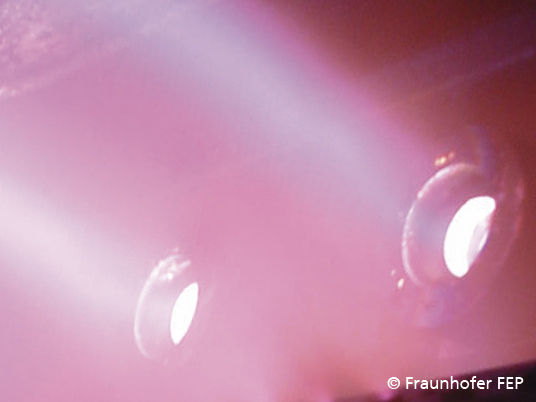
Highly productive vacuum coating process of Fraunhofer FEP
Fraunhofer FEP
Scientists at the Fraunhofer Institute for Electron Beam and Plasma Technology FEP have developed a novel vacuum coating process which in addition to the existing vacuum processes such as magnetron sputtering and high-rate evaporation makes the deposition of new layer systems and materials with very high coating rates possible.
In the hollow cathode arc PECVD process (short: arcPECVD) a reactive gas, such as hexamethyldisiloxane (HMDSO), enters the reaction chamber and is effectively excited, ionized and decomposed by means of hollow cathode arc plasma. Through this process a siliceous layer is deposited on the substrate. Depending on the process parameters comparatively soft and elastic plasma polymeric layers but also inorganic, more rigid and dense layers can be achieved. For instance, in order to build a permeation barrier usually a layer stack is used, where a relatively thick, elastic smoothening layer is embedded in between the actual functional layers. So far, hitherto existing PECVD processes have not been feasible enough for the deposition of these interlayers due to their low coating rates. As alternatives lacquering processes have been used, which however require the transfer out off and back into the vacuum chamber. With the arcPECVD process a tool is now available, which is predestined for these applications and which can be applied in-line with other PVD processes.
The process, which is carried out at the low pressure of 0.1 … 5 Pa, can be effortlessly combined in a coating system with other PVD processes such as magnetron sputtering or electron beam deposition. This makes it possible to apply entire layer stacks in-line in only one vacuum run in roll-to-roll systems: this results in enormous savings in terms of time and money. The arcPECVD process was developed at the Fraunhofer FEP using the institute’s very own plasma sources and demonstrates good process stability. During a coating time of more than 2.5 hours, a constantly high coating rate of 2000 nm ∙ m/min ± 1.5 % could be achieved.
The Fraunhofer FEP’s hollow cathode plasma sources have already been approved in the industrial sector. They have been in use in the production of packaging films in widths of up to 2.85 meters for the past five years.
Dr. Steffen Günther, a specialist for PECVD processes at Fraunhofer FEP, sees enormous application potential for the arcPECVD: “We have already been able to show that PECVD layers are able to significantly reduce the layer stress in optical layer stacks. I see a great potential for example in the combination of the arcPECVD with the electron beam deposition of titanium oxide which would allow the highly productive – and as a result cost-effective – production of optical layer systems. Other application areas are permeation barriers for photovoltaic modules and organic electronics. The arcPECVD process is ready and waiting to be adapted to specific layer and customer demands within the framework of joint development projects with partners from both the industrial and research sectors.”
Most read news
Other news from the department science
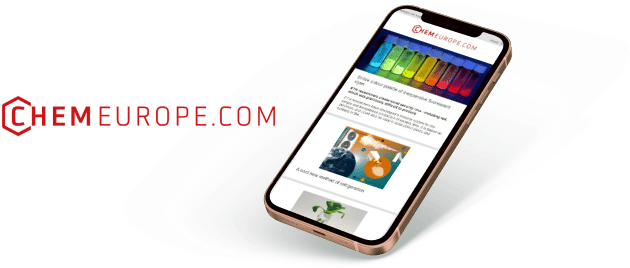
Get the chemical industry in your inbox
By submitting this form you agree that LUMITOS AG will send you the newsletter(s) selected above by email. Your data will not be passed on to third parties. Your data will be stored and processed in accordance with our data protection regulations. LUMITOS may contact you by email for the purpose of advertising or market and opinion surveys. You can revoke your consent at any time without giving reasons to LUMITOS AG, Ernst-Augustin-Str. 2, 12489 Berlin, Germany or by e-mail at revoke@lumitos.com with effect for the future. In addition, each email contains a link to unsubscribe from the corresponding newsletter.