Formation of self-supporting porous membranes and tiny ceramic rings
02-Oct-2003
Wetting is the magic word behind the clever new method developed by Hui Xu and
Werner A. Goedel of the University of Ulm and BASF AG. The researchers used
their technique to produce self-supporting membranes with highly uniform pores
and, in a second step, microscopically small ceramic rings. These rings are
potentially useful as structural elements for microelectronic devices.
Thin membranes with precisely controlled pores are commonly made by dissolving
away one component of a structured matrix. Until now, the problem with this has
been that the membranes, which are formed on a solid support, are then difficult
to separate from it. Xu and Goedel decided to use a water surface as their
support. Water surfaces cannot usually be covered by organic substances; nearly
all non-water-miscible organic liquids form drops (fat globules), not an even
layer, on a water surface. This is where a new principle, "particle-assisted
wetting", comes into play. When the organic liquid is mixed with tiny
hydrophobized silica gel particles, the particles bind to the water surface,
pulling the organic liquid along to form a thin, mixed layer on the surface of
the water. The researchers use particles whose diameter allows them to stick out
above and below the layer. The liquid, an acrylate, is then cross-linked
(polymerized) by irradiation with light. Hydrofluoric acid vapors then dissolve
the embedded silica spheres out of the layer, leaving behind a polymer membrane
that is thin and highly porous, while being robust enough to be transferred from
one support to another or to be stretched, whilst remaining self-supporting,
over porous substrates. The uniformity of the pore size makes this new type of
membrane suitable for use in separation techniques such as ultra- or sterile
filtration.
The membrane can also serve as a "ring-mold". When the polymer membrane on a
solid support is dipped into a solution of an organic titanium compound and
dried, and the titanium compound is converted into titanium oxide by a chemical
reaction with moist air, a thin ceramic layer is formed on the walls of the
pores. Subsequent heating removes the membrane, leaving behind lots of little
rings, whose outer diameter corresponds to the size of the pores in the
membrane. The secret behind this technique lies in the wetting. The dipping
solution selectively wets the interior of the pores, but not the outer surface
of the membrane. The reason for this may be that the silica gel particles
"stamp" a different chemical structure onto the pores' surfaces during the
cross-linking of the acrylate. If the polymer membrane is dunked into the
solution without a solid support, the rings end up firmly attached to each
other, because the slowly deteriorating membrane deforms the rings such that
they can be sintered together. The result is a stable ceramic membrane made of
connected rings.
Most read news
Other news from the department science
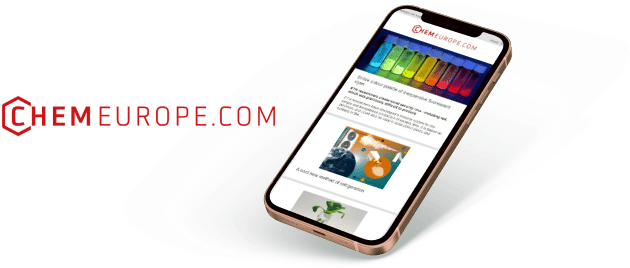
Get the chemical industry in your inbox
From now on, don't miss a thing: Our newsletter for the chemical industry, analytics, lab technology and process engineering brings you up to date every Tuesday and Thursday. The latest industry news, product highlights and innovations - compact and easy to understand in your inbox. Researched by us so you don't have to.