Product Innovation Holds the Key to Faster Growth for Plastics in Automotive Applications
06-Sep-2001
Resin suppliers, together with OEMs and processors, must continue to
introduce innovative products and technologies to further drive the
development of new applications for engineering plastics in the automotive
market, according to a new study from Frost and Sullivan. Developing
technologies that are credible alternatives to traditional materials such
as metal and glass can be expected to open up new market opportunities.
David Platt, Senior Plastics Industry Analyst at Frost & Sullivan explains;
"lower growth is predicted for engineering plastics in the automotive
industry during the period 2001-2007 because of the downturn in European
car production and also due to the growing market maturity for plastics in
a number of important automotive applications. Car producers will however
continue to strive for lower costs, weight reduction and fuel economy,
while at the same time introducing more comfort and safety features into
their products. These requirements, combined with technological
innovation, will drive the development of new applications for engineering
plastics in passenger cars."
There are many examples of how new technologies are being developed to
create opportunities for plastics in the automotive market. Some of the
most notable are:
· GE Plastics Noryl products based on blends of polyphenylene oxide have
the advantages of better heat resistance and conductivity, which has led to
their replacement of other polymers in bumper systems. Noryl's better heat
resistance and lower odor emissions also gives it an advantage over PC/ABS
for car instrument panels.
· Bayer's "hybrid technology", binding plastics and steel, which lowers
weight and module costs and creates a high load-bearing capacity while
allowing high energy absorption has led to its use in components for doors,
seats, front ends and bumper brackets.
· Exatec's automotive glazing systems based on polycarbonate are thought
to give a weight saving of around 40% compared with glass. Product and
systems development is focussed on the rear and side windows, which should
be ready for market testing in 2002.
In 2000, the total tonnage of engineering plastic used in passenger cars
was 1.4 million tonnes, the study forecasts that in 2007 this will have
risen to 1.7million tonnes ? representing a 2.6 % compound annual growth
rate. This is significantly lower than the previous 4 years when unit rate
growth averaged nearly 6% per annum. Use of plastics in electrical and
lighting systems and under the bonnet applications will show the fastest
growth rates, whilst the market shares for both interior and exterior
plastics will decline.
polypropylene is by far the most commonly used resin and is found mainly
inside the car for instrument and door panels. However, over the forecast
period it is expected to lose market share to other polymers such as PC/ABS
blends.
This new study is an in-depth analysis of trends in the use of all types of
engineering plastics, throughout the range of automotive application areas.
It gives an insight into the competitive structure of the market and makes
strategic recommendations for future success in this market.
Sales Contact
European Engineering Plastics in Automotive Applications (report code
3872-39) published September 2001 is available to purchase from: Frost &
Sullivan, 4100 Chancellor Court, Oxford Business Park, Oxford, OX4 2GX, UK.
Sales Contact: Bill Stringer +44 (0) 1865 398651,
bill.stringer@fs-europe.com
Most read news
Topics
plastics
glass
Frost & Sullivan
GE - Plastics
Exatec
Bayer
Replacement
reductions
polypropylene
emissions
conductivity
absorption
Organizations
Frost & Sullivan
Other news from the department business & finance
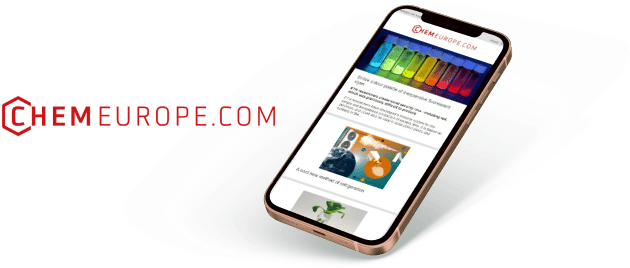
Get the chemical industry in your inbox
From now on, don't miss a thing: Our newsletter for the chemical industry, analytics, lab technology and process engineering brings you up to date every Tuesday and Thursday. The latest industry news, product highlights and innovations - compact and easy to understand in your inbox. Researched by us so you don't have to.