Virtual lab calculates optimal lubricant composition
Extending lubricant lifespan: Sensor system developed for real-time monitoring
Mechanical bearings and gearboxes — like those used in electric vehicles and wind farms — are often treated with lubricants to avoid friction and wear. However, these components might be under voltage. This would impair the effectiveness of the lubricants to such a degree that the tribological contacts are damaged. As part of the Lube.Life joint research project, researchers at the Fraunhofer Institute for Mechanics of Materials IWM have developed a virtual lubricant lab, which can be used to predict the effects of electrical fields on lubricant stability. As a result, customized formulations for new lubricants can be created.
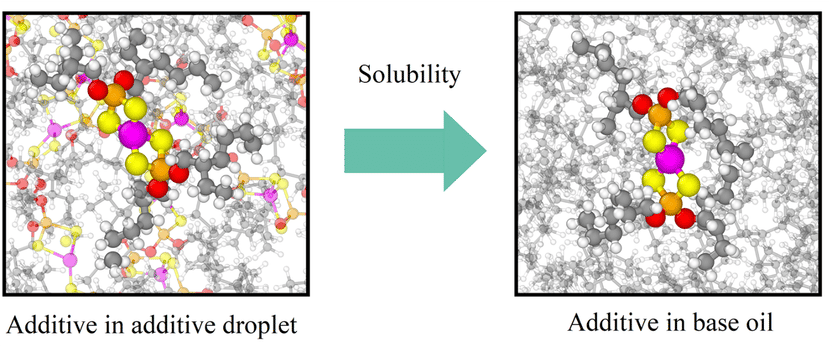
Atomistic calculation of the solubility of additives in the virtual lubricant lab
© Fraunhofer IWM
In tribological systems, such as bearings, gearboxes and seals, electrical fields impact the efficacy of lubricants and thus the lifespan of the components used. Electrical charge is of particular importance in electric vehicles and wind farms. These sectors use large amounts of lubricant on rotor bearings, for example, to reduce friction and thus wear. The lubricant may degrade over time, which, in the worst-case scenario, could lead to total system failure. One cause of this degradation is the use of additives in lubricants, which can be affected by the presence of electrical fields. The short- or long-term separation of these additives may lead to electrical breakdown and component damage. This problem is increasingly taking center stage against the backdrop of the energy transition.
Up to now, offshore wind farms have only monitored lubricants during regular maintenance. Inspections are particularly difficult to carry out in the winter months due to the weather conditions. The Lube.Life joint research project has therefore developed a sensor system, consisting of infrared, moisture, acoustic and friction sensors, and evaluation electronics to monitor these lubricants in real time. Sensor data, predictive online algorithms and simulated analysis data are combined and used to create an overall assessment of the lubricant.
Extending lubricant lifespan
The sensor signals are collected in software developed by the project coordinator, QASS, before undergoing analysis in the central part of the software — the virtual lubricant lab. This innovation enables existing lubricants to be assessed based on their electrotribological suitability. It also allows for the qualification of lubricant additives and a preliminary assessment when designing a new lubricant. A key objective is stabilizing the lubricant by subsequently adding suitable additives to extend the use phase. “The virtual lubricant lab offers many different types of support. It helps to change the additive composition in a lubricant in cases where, for example, an additive is no longer available, or its use is legally prohibited for environmental reasons. The same applies if a lubricant no longer works properly because an additive has formed droplets and the lubricant’s dielectrical properties have changed, meaning that adjustments are required,” explains Prof. Michael Moseler, head of the Tribology business unit at Fraunhofer IWM in Freiburg. “To date, our project partner ASC Görlach has illustrated this using a heuristic computational model. We were able to use molecular dynamics to show that a reduction in energy of solvation due to strong electrical fields can cause droplets to form. These droplets can significantly reduce a lubricant’s dielectric strength.”
However, researchers at Fraunhofer IWM have also been able to physically calculate a number of other lubricant parameters. These include viscosity, thermal conductivity, and chemical reactivity with surfaces. This makes it possible to determine what effect adding a certain amount of a specific additive to a lubricant will have. “The sensor system will draw real-time conclusions about the composition of the lubricant. By interacting with the virtual lubricant lab, a variety of measures can be taken, ranging from simple notification and triggering of a maintenance order to the automated additional dosing of additives,” states the researcher in regard to the interplay of components.
The future areas of application are numerous: In addition to monitoring wind farms, a real-time, decentralized analysis and forecasting system for lubricants could be used to upgrade industrial and production facilities, as well as power plants. Instead of adhering to inflexible maintenance periods, operators will be able to increase maintenance flexibility, adapting to every situation. The virtual lubricant lab even plays to its strengths in the design of lubricants, providing important information for creating new formulations.
Project partners:
- ASC-Görlach
- Fraunhofer IWM
- FUCHS LUBRICANTS GERMANY GmbH
- HYDAC Electronic GmbH
- Kompass Sicherheitstechnik
- QASS GmbH (Verbundkoordinator)
- Schaeffler Technologies AG
Other news from the department science
These products might interest you
Most read news
More news from our other portals
See the theme worlds for related content
Topic world Sensor technology
Sensor technology has revolutionized the chemical industry by providing accurate, timely and reliable data across a wide range of processes. From monitoring critical parameters in production lines to early detection of potential malfunctions or hazards, sensors are the silent sentinels that ensure quality, efficiency and safety.
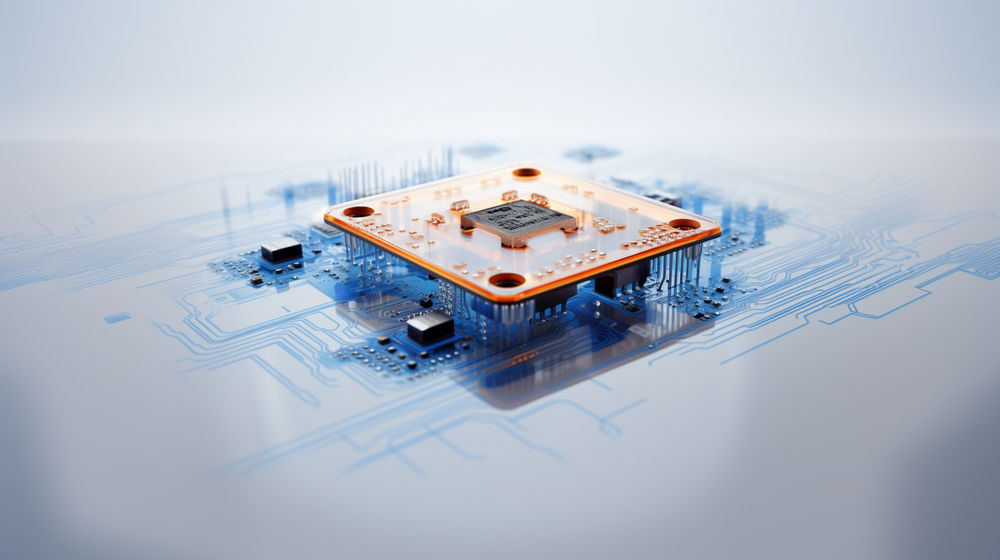
Topic world Sensor technology
Sensor technology has revolutionized the chemical industry by providing accurate, timely and reliable data across a wide range of processes. From monitoring critical parameters in production lines to early detection of potential malfunctions or hazards, sensors are the silent sentinels that ensure quality, efficiency and safety.