Fifty years of propionic acid manufacturing at BASF
A rather acidic success story started at BASF 50 years ago: in the summer of 1960, the company brought on stream the first large-scale manufacturing plant for propionic acid at its integrated Ludwigshafen Verbund site. The inauguration of another facility that produces this carboxylic acid followed at the Nanjing site in China in 2005. Having expanded the annual capacity at these sites in 2009, which brought its total annual capacity to 149,000 metric tons, BASF is now one of the world’s major propionic acid manufacturers. This organic acid, which also occurs naturally, is valued as a preservative for feedgrain and as a building block for synthesis, for example in the production of pharmaceuticals, crop protection products and plastics. BASF has to date produced about 2.4 million metric tons of propionic acid.
In 1941, Professor Walter Reppe, a BASF chemist always keen on experimenting, managed to synthesize propionic acid from ethylene. Ten years later, BASF built a pilot plant, and the production started just another year later. Designed for 1,200 tons per annum, the plant was soon unable to meet the constantly rising demand. So in 1960 a new large-scale plant was built that continues to make propionic acid today.
“The synthesis is still based on the principle developed by Reppe, but over the years we have optimized and expanded the plant so that production is now much more efficient,” explained Dr. Bernd Bartenbach, who is responsible for the production of propionic acid at the Ludwigshafen site.
The importance of propionic acid is quite different now from what it used to be in Reppe’s time. In those days, nearly 70 percent of the total volume was used to make vinyl propionate. Processed into polymer dispersions, the acid was ultimately used as a protective exterior paint for buildings.
Today, the acid’s main field of application is in preserving feedgrain. Propionic acid keeps feeds fresh for a long time because it prevents molding. Feedgrain preservation based on propionic acid offers clear economic and ecological benefits over other methods, as an ecoefficiency analysis confirms. This study shows that using this acid to preserve feedgrain is much more eco-efficient than feedgrain preservation by means of drying or storage in air-tight silos. BASF markets preservatives based on propionic acid under the trade names Lupro-Grain® and Luprosil®.
Calcium propionate, a propionic acid salt, keeps sliced and packaged bread fresh for longer. In addition the organic acid is used to produce medicines, crop protection agents and solvents as well as thermoplastics. “Propionic acid is a great example of the versatility of our more than 600 intermediates that prove their benefits in our daily lives,” said Dr. Beate Ehle, President of BASF’s Intermediates division, and continued: “It also illustrates perfectly our innovative capacity and our ability to grow with our customers on a global basis.”
Other news from the department business & finance
These products might interest you
Most read news
More news from our other portals
See the theme worlds for related content
Topic world Synthesis
Chemical synthesis is at the heart of modern chemistry and enables the targeted production of molecules with specific properties. By combining starting materials in defined reaction conditions, chemists can create a wide range of compounds, from simple molecules to complex active ingredients.
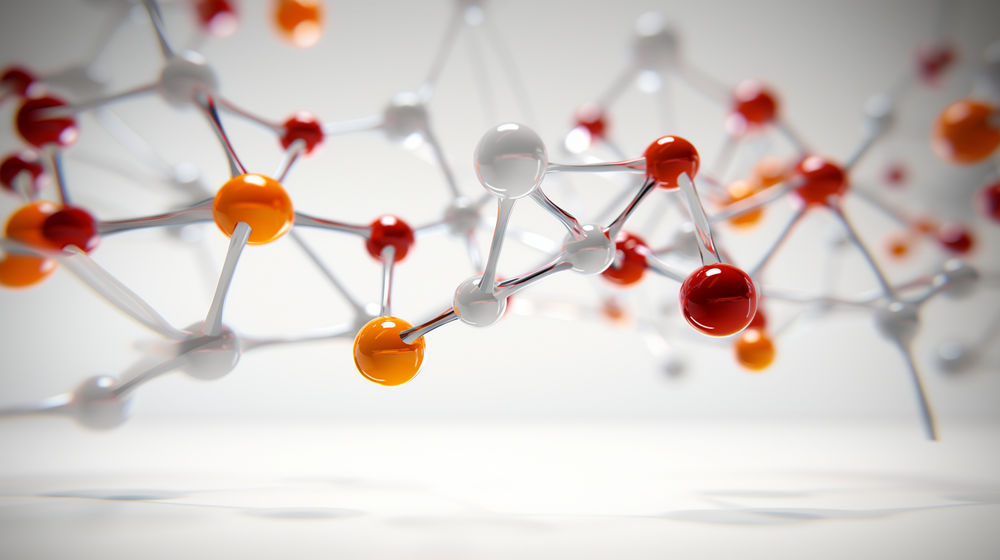
Topic world Synthesis
Chemical synthesis is at the heart of modern chemistry and enables the targeted production of molecules with specific properties. By combining starting materials in defined reaction conditions, chemists can create a wide range of compounds, from simple molecules to complex active ingredients.