BASF Coatings: CO2 emission reduced by 50 percent since 1990
Since 1990 BASF Coatings AG has reduced emissions of the "greenhouse gas" carbon dioxide at its Münster site by 50 percent or, when taking into account the output of the plant, by as much as about 62 percent. With this reduction, the company has far exceeded the targets set by both the German government and the UN. The agreement which the international community - with the exception of the USA - signed on 12 November at the UN Climate Conference in Marrakech is a binding legal framework for the implementation of the Kyoto Protocol: the target of the climate change convention is to achieve a progressive reduction in emissions of greenhouse gases by an average of 5.2 percent (compared to 1990) by 2012. The German government had set itself the target of a 21 percent reduction, of which 18 percent has so far been achieved.
With the aim of establishing sustainable development, BASF Coatings has for many years been continuously reducing its emissions into the air, water and soil. Two key elements of this corporate policy are the systematic reduction of greenhouse gases and economical energy management. "At our Münster site, we have halved our CO2 emissions since 1990. This excellent result has been achieved by a wide variety of measures and by investment in almost every installation. These measures included modernization of the distillation plant with an efficient heat recovery system, the decentralization of heat supply, with resulting avoidance of conveyance losses, and carefully calculated optimizations of the building ventilation systems. In addition, the improved insulation of the buildings has also had a positive effect," explains Dr. Peter Bachhausen, head of BASF Coatings' Environment and Safety unit. In individual installations, a combination of air recirculation and heat recovery has been implemented, for example in the finished products store. Here, only 20 percent of the total air required is replaced by fresh air, whilst 80 percent of the air is maintained in recirculating mode. Sensors in the plant constantly monitor the air quality. In addition, the fresh air supplied from outside is heated in heat exchangers by the air extracted from the interior. This ingenious heat exchange system reduces the thermal energy required in this area by more than 90 percent. Other investment projects include for example the ventilation systems in the production installations, where energy consumption has been considerably reduced. "By modifying our production processes and working conditions, we will further improve ventilation efficiency in our installations and will therefore further cut back our energy consumption. With the measures already taken and the measures planned for the future, we are making a major contribution to the protection of resources and climate whilst also permanently reducing the operating costs of our installations."
Other news from the department politics & laws
These products might interest you
Most read news
More news from our other portals
See the theme worlds for related content
Topic world Sensor technology
Sensor technology has revolutionized the chemical industry by providing accurate, timely and reliable data across a wide range of processes. From monitoring critical parameters in production lines to early detection of potential malfunctions or hazards, sensors are the silent sentinels that ensure quality, efficiency and safety.
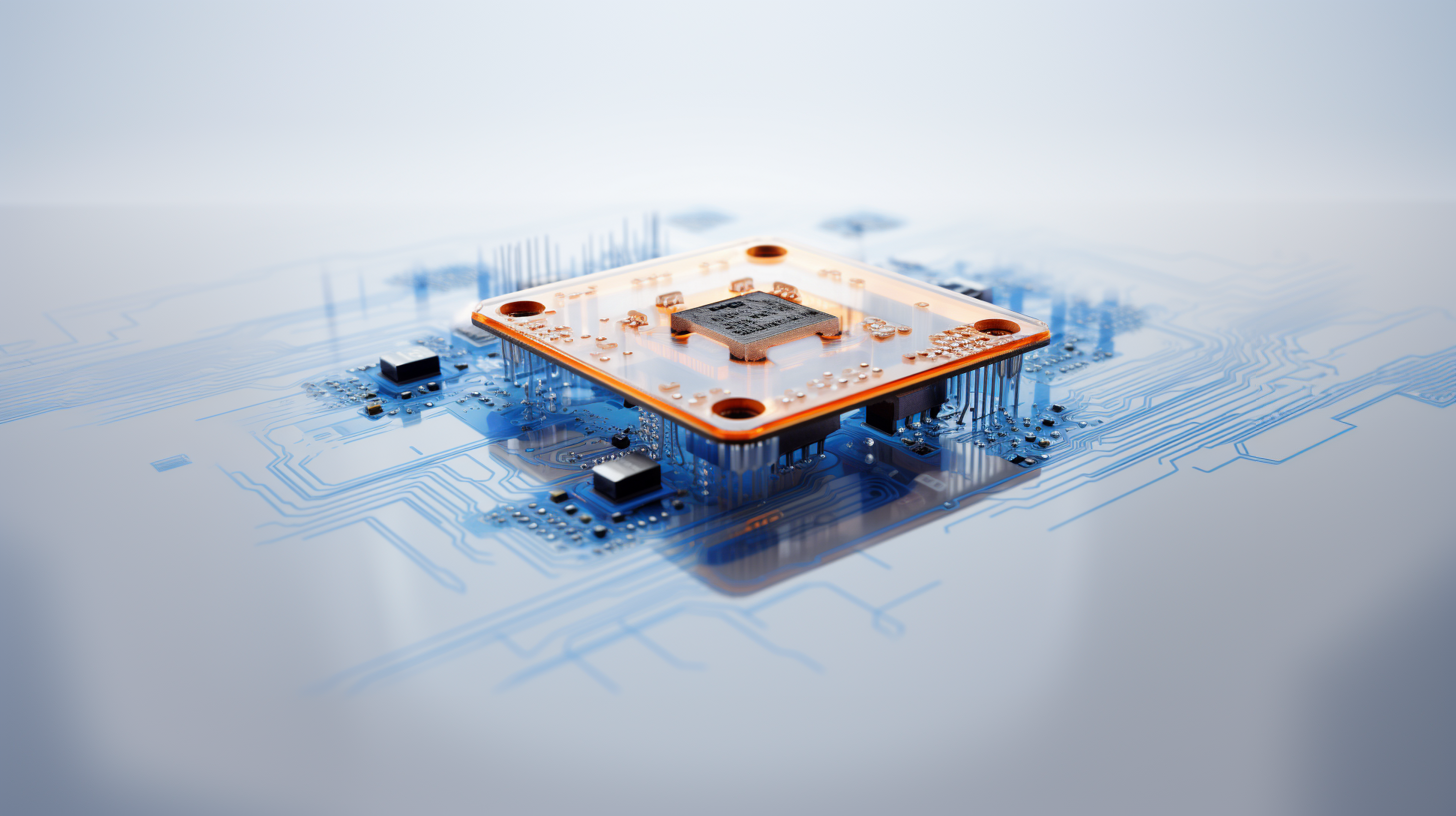
Topic world Sensor technology
Sensor technology has revolutionized the chemical industry by providing accurate, timely and reliable data across a wide range of processes. From monitoring critical parameters in production lines to early detection of potential malfunctions or hazards, sensors are the silent sentinels that ensure quality, efficiency and safety.