Ultramid - the missing link
BASF nylon to be used in engine throttle systems
BASF and the car components maker MGI Coutier have succeeded in developing a plastic throttle system.
Over the past thirty years more and more metallic automotive components-everywhere on the vehicle, not just in the engine compartment-have been replaced by plastic ones. BASF has been making a name for itself since 1972 through its development of plastic intake manifolds, a major component in the engine intake system. On today's modern vehicles, almost all intake system components are made from plastic-air cleaner housing, resonators, air mass sensor housing and of course the intake manifold. However, one component that has defied conversion to plastic has been the throttle body housing-until now that is.
Engineers from MGI Coutier S.A. (Champfromier/France) and BASF's European Engineering Plastics business unit have developed two throttle bodies molded from Ultramid®, the nylon by BASF. Ultramid A3WG6, a nylon 66 with 30 percent glass fibers, is used for the throttle body of the Renault 1.4 liter E7J engine in the Clio, Megane and Kangoo. Ultramid A3WG7, containing 35 percent of glass fibers, is used in the case of the PSA 1.7/2.0 liter EW engines in the Peugeot 307/406/607, Citroën Xantia/Xsara and in the new C5. Both parts - E7J and EW engine throttle - feature a mechanically operated throttle valve. MGI Coutier is a direct supplier of components to Renault, PSA, Ford, VW, GM and Fiat.
The Ultramid housing is capable of withstanding the mechanical loads and is chemically resistant to automotive fuel and lubricants. In addition, its intricate design ensures the system remains airtight in the specified temperature range of - 40 to + 140 Celsius.
Like other parts, the plastic throttle body has a number of advantages over conventional alloy versions. First, weight reductions of up to 50 percent mean smaller inertial forces and improved vibrational behavior. Second, cost savings: the plastic part is cheaper to produce since it integrates many previously separate components into a single moulding. And finally, plastics give engineers much greater design freedom- essential when it comes to making complex parts. In the case of the throttle, that led to better operating performance.
Moreover, material compatibility will offer the potential for further developments: the nylon throttle system may be directly integrated into the nylon air intake manifold.
Most read news
Organizations
Other news from the department research and development
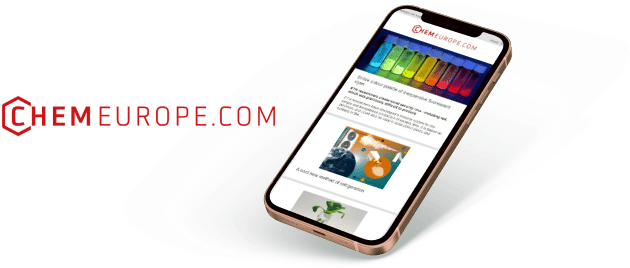
Get the chemical industry in your inbox
From now on, don't miss a thing: Our newsletter for the chemical industry, analytics, lab technology and process engineering brings you up to date every Tuesday and Thursday. The latest industry news, product highlights and innovations - compact and easy to understand in your inbox. Researched by us so you don't have to.