Market premiere of thermoformable sheets made from polyamide 6
A cost-effective alternative to injection molding for small-scale manufacture
Leverkusen – For the first time, thermoformable sheets made from polyamide 6 (PA 6) are also available on the semi- finished products market, distributed by Sustaplast KG, a Lahnstein, Germany-based specialist for high-performance semi-finished products, under the brand name of SUSTAVACU®. They are manufactured from Durethan® DP2-2140/15 Z H2.0, a Bayer product. "The key property of the polyamide, which is reinforced with glass fibers and modified to make it impact resistant, is its high pseudoplasticity. This provides the necessary degree of melt stiffness, which is what actually enables the sheets to be thermoformed," explains Dr. Karsten Idel, who is responsible for research into semi-crystalline thermoplastics in Bayer's plastics Business Group.
"Their balanced property profile at a high level means that the PA 6 sheets fill a niche in the field of high-performance semi- finished products which was previously unfilled," explained Norbert Hendel, Sustaplast's sales manager, responsible for the semi-finished products business in Germany. What is more, thermoforming is a much less complex industrial process and – particularly when it comes to small-scale production runs – significantly more cost-effective than injection molding, the process that until now has been used to manufacture most polyamide 6 components.
Specialists from Adolf Illig Maschinenbau GmbH & Co. KG, Heilbronn, Germany, a leading manufacturer worldwide of thermoforming machines, were also impressed by the new material. Using one of their UA 100g thermoforming machines, they thermoformed the model of a Porsche 911 from 6 mm thick sheets, and put the material through its paces. "What won us over, in addition to the easy processing and the mechanical properties, was the high accuracy in reproduction of detail exhibited by the by the material and the attractive surface quality of the components," recalls Sven Engelmann, an engineer in basic development and application technology at Illig. Following the encouraging tests, the company wants to include the grade, as the first polyamide 6, in its in-house list of recommended thermoformable materials.
There is great potential for using the new generation of semi- finished products, above all in components that are exposed to high continuous service temperatures of up to 140 ºC. The material can also withstand short-term temperature peaks of 170 ºC without losing the good balance of stiffness, strength and impact strength. A further advantage is the high resistance to a number of chemicals. All of these assets mean that the sheets are ideal, in particular, for the manufacture of components for the engine compartment of cars and HGVs – for example engine shrouds, sound proofing components and underbody panels. Other potential applications include, for example, HGV side panels as underride protection and transport containers in mechanical engineering.
Sustaplast is initially offering the PA 6 sheets in thicknesses of two to six millimeters, colored black. You can request information from Sustaplast about the new semi-finished products by faxing +49 2621 69 31 58. An overview of the properties of the pseudoplastic Bayer polyamide is available in the application technology information sheets "Durethan KU2 2140/15 and Durethan DP2 2140 15 Z H2.0 for sheet extrusion and thermoforming applications" (ATI 5310) that can be downloaded in English and German from the Plastics Business Group site www.plastics.bayer.com/AG/DE/ neulit.jsp.
Topics
Organizations
Other news from the department research and development
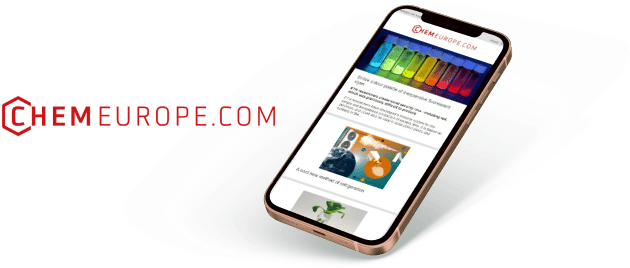
Get the chemical industry in your inbox
By submitting this form you agree that LUMITOS AG will send you the newsletter(s) selected above by email. Your data will not be passed on to third parties. Your data will be stored and processed in accordance with our data protection regulations. LUMITOS may contact you by email for the purpose of advertising or market and opinion surveys. You can revoke your consent at any time without giving reasons to LUMITOS AG, Ernst-Augustin-Str. 2, 12489 Berlin, Germany or by e-mail at revoke@lumitos.com with effect for the future. In addition, each email contains a link to unsubscribe from the corresponding newsletter.
Most read news
More news from our other portals
Last viewed contents
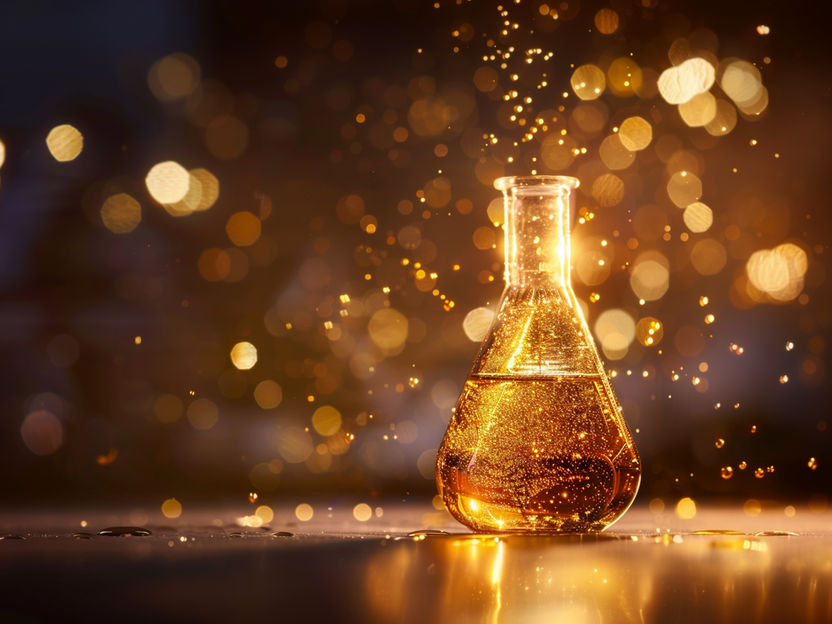
From waste to value: The right electrolytes can enhance glycerol oxidation - "Our research could help to convert biomass by-products into valuable chemicals more efficiently"
Univar’s acquisition of Quaron Group Benelux is ready for Closing

New mid-infrared laser system could detect atmospheric chemicals
Zomepirac
Helvetica_Chimica_Acta
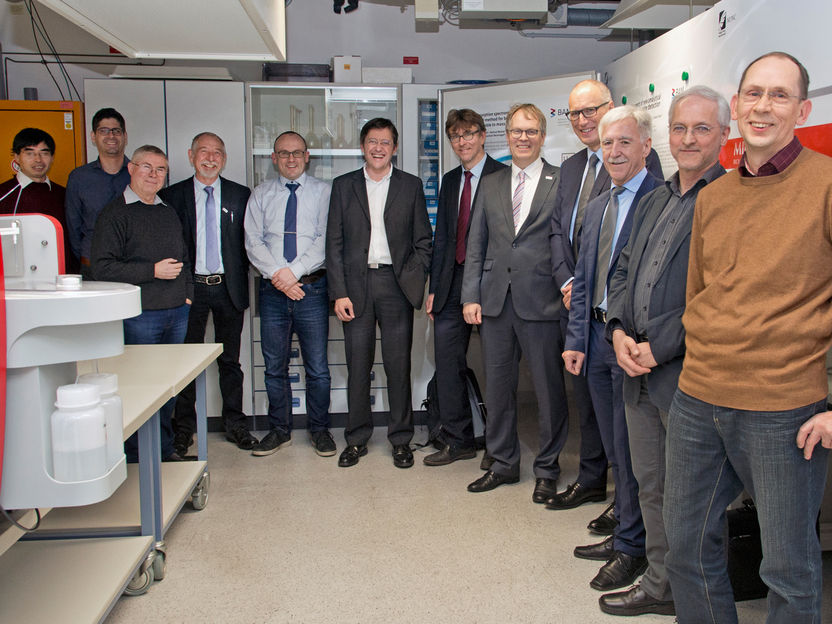