Economical energy storage for the electric car of tomorrow
Dry electrode coating technology allows environmentally friendly battery cell production
Advertisement
Researchers at the Fraunhofer Institute for Material and Beam Technology IWS in Dresden have developed a new production process with the aim of efficient and environmentally friendly future battery production. They coat the electrodes of the energy storage cells with a dry film instead of liquid chemicals. This simplified process saves energy and eliminates toxic solvents. A Finnish company is currently successfully testing the new IWS technology in practice.
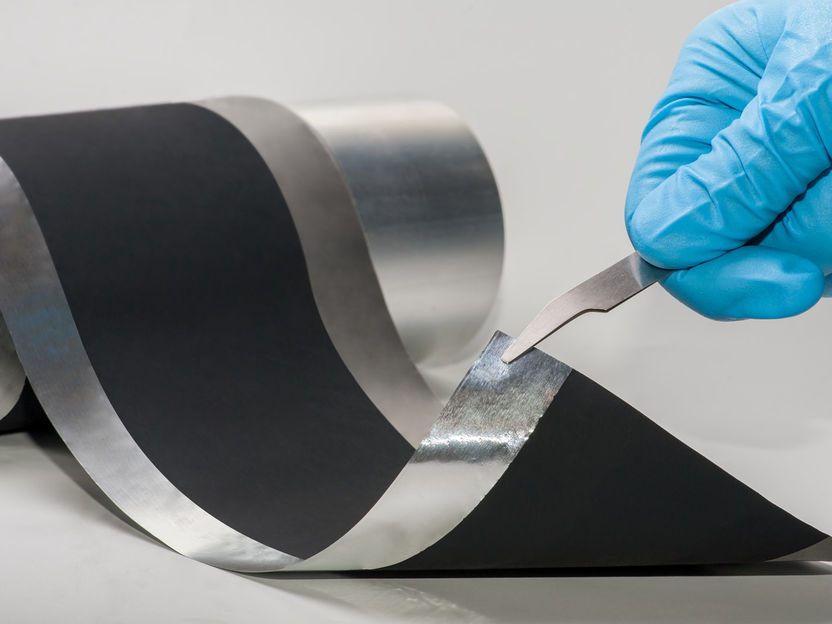
This is what the electrodes coated with the new dry transfer coating technology look like. Fraunhofer IWS process enables battery electrodes to be produced on a pilot scale without using toxic solvents.
© Fraunhofer IWS Dresden
Better and more cost-efficient production methods for energy storage are increasingly in demand, especially in Germany: All major automobile manufacturers have launched ambitious electric vehicle programs that will ensure a sharp rise in demand for batteries. So far, German companies have been purchasing the cells for this purpose in Asia. There are two main reasons driving this trend: Asian technology groups have many years of experience in the mass production of battery cells and a lot of energy is consumed in these processes. Production at locations with high electricity prices, such as Germany, is, therefore, very high-cost.
No more toxic solvents – lower electricity costs
It is exactly this fact the Saxon Fraunhofer engineers want to change: “Our dry transfer coating process aims to noticeably reduce the process costs in electrode coating,” emphasizes IWS project manager Dr. Benjamin Schumm. “Manufacturers can eliminate toxic and expensive solvents and save energy costs during drying. In addition, our technology also facilitates the use of electrode materials that are difficult or even impossible to process wet-chemically.” But exactly these materials are needed for future batteries with higher energy density. “For all these reasons, we think that our technology can help to achieve internationally competitive battery cell production in Germany and Europe.”
Pilot plant successfully started in Finland
This potential is also seen by Fraunhofer's Nordic partners: The Finnish battery company "BroadBit Batteries", together with IWS, has commissioned a pilot plant in its Espoo factory, which coats electrodes with dry electrode material instead of wet pastes, as has been common in industry up to now. BroadBit uses it to produce new types of sodium ion batteries. "The demand for our technology is high, even in Germany," reports Benjamin Schumm. On a laboratory scale, the IWS can already coat electrode foil with a remarkable production speed of several meters per minute. In this respect the Dresden engineers can show the potential for transferring the technology to the production scale.
Limits of classic wet chemistry
Until now, cell producers have mostly coated their battery electrodes in a complex wet-chemical process. First, they mix the active materials, intended later to release the stored energy, with additives to create a paste. In this process they add organic solvents, which are expensive and usually toxic. In order to protect operators and the environment, elaborate precautions for occupational safety and reprocessing are necessary. Once the paste has been applied to thin metal foils, a further expensive process step begins: Dozens of meter long heating sections dry the coated films before they can be further processed. This drying procedure usually causes high electricity costs.
Binding molecules form a cobweb
The new film transfer technology for dry electrode coating, on the other hand, operates without these ecologically damaging and expensive process steps: The IWS engineers mix their active material with binding polymers. They process this dry mixture in a rolling mill known as "calender". The shear forces in this system tear entire molecular chains out of the binder polymers. These "fibrils" join with the electrode particles as in a spider web. This provides the electrode material with stability. The result is a flexible dry electrode material layer. In the next step, the calender laminates the 100 micrometer thick film directly onto an aluminum foil, thus creating the battery electrode.
On the way to the solid state fireproof battery
"In this way, we are also able to process materials for new battery generations where classical processes fail," says Benjamin Schumm. These include, for example, energy storage systems that use sulfur as active material or solid-state batteries which employ ion-conducting solids instead of flammable liquid electrolytes. "These batteries will be able to store more energy in the same volume than today's lithium-ion batteries," says the IWS scientist with a view to the future. "However, these solid electrolytes can lose their functional properties in contact with solvents. A solvent-free coating process is significantly better qualified to produce these storage media." On the way of processing electrodes for all solid state batteries the researchers have reached one important milestone by applying their dry film technology using extremely low binder contents. They have recently published their results in ScienceDirect.
Process could replace classic paste processes
The Dresden engineers now aim at enhancing their technology in cooperation with industrial partners in order achieve its breakthrough. In the BMBF-funded "DryProTex" project, for example, they are further developing the dry transfer coating process together with the companies Saueressig, INDEV, Netzsch Trockenmahltechnik and Broad-Bit Batteries. The partners expect a fundamental change in battery production: "The technology offers great potential to replace conventional processes for paste-based electrode production on the long run," concludes Benjamin Schumm. In the DryProTex project material, process and equipment developments are conducted with the aim of realizing process design for industrial scale dry cathode production.
Other news from the department science
These products might interest you
Most read news
More news from our other portals
See the theme worlds for related content
Topic World Battery Technology
The topic world Battery Technology combines relevant knowledge in a unique way. Here you will find everything about suppliers and their products, webinars, white papers, catalogs and brochures.
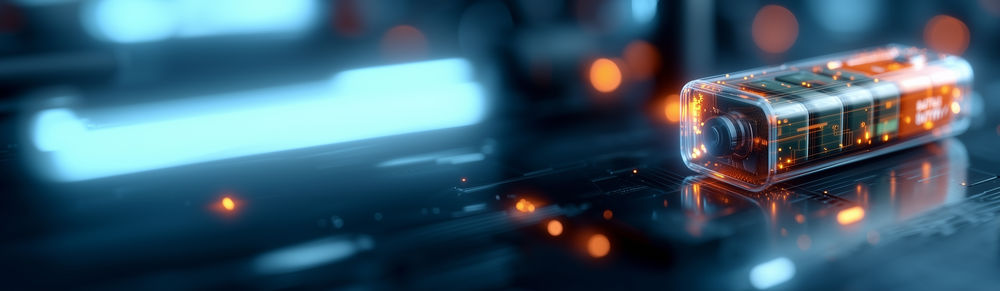
Topic World Battery Technology
The topic world Battery Technology combines relevant knowledge in a unique way. Here you will find everything about suppliers and their products, webinars, white papers, catalogs and brochures.