When batteries become foam
New concept for improved battery recycling
Efficiently recycling batteries and reintegrating the recovered materials into production is still an apparently unsolvable problem for industry. That's why researchers around the world are looking for new approaches. One of them is Anna Vanderbruggen. The PhD student at the Helmholtz Institute for Resource Technology Freiberg (HIF) - an institution of the Helmholtz-Zentrum Dresden-Rossendorf (HZDR) - developed a concept to recycle Graphite from used lithium-ion batteries.
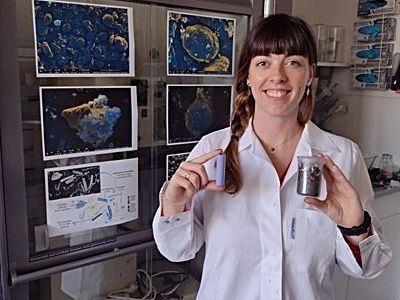
HIF PhD student Anna Vanderbruggen
HZDR/HIF
Electro mobility increases the demand for lithium-ion batteries - and leads to an enormous global demand for critical materials such as nickel, cobalt, lithium and natural graphite, which, on the other hand, are not infinitely available on our planet, and, on the other hand, are often mined under poor conditions. Therefore, the development of efficient recycling technologies and the integration of the recovered materials into battery cell production is absolutely essential. The goal is to close material cycles with efficient approaches.
A very relevant but also very critical material for lithium-ion batteries is graphite. Due to the energy transition in the mobility sector, graphite will remain one of the determining materials in battery production in the coming decades. However, natural deposits of graphite that can be mined economically are rare. Furthermore, recycling companies are currently unable to recover graphite. Therefore, it ends up as waste or is used as a reductant agent during the recycling process. Anna Vanderbruggen has taken up this challenge and developed a concept for "recovering graphite from spent lithium ion batteries", which is also the subject of her PhD thesis.
“My approach uses the method of froth flotation, which is proven in the raw materials industry, to recycle graphite. Froth flotation is an established and efficient process for separating valuable minerals from waste rock for particle sizes of about 10 to 200 micrometer. The process is based on the selective hydrophobisation, i.e. water-repellent property, of minerals and the adhesion of these particles to gas bubbles, which are subsequently discharged via a foam. Therefore, surface properties, but also other particle properties such as size and morphology, are the key separation characteristics for froth flotation. Adding a froth flotation stage allows the metals and graphite to be recovered together,” Anna Vanderbruggen explains her concept.
Other news from the department science
These products might interest you
Most read news
More news from our other portals
See the theme worlds for related content
Topic World Battery Technology
The topic world Battery Technology combines relevant knowledge in a unique way. Here you will find everything about suppliers and their products, webinars, white papers, catalogs and brochures.
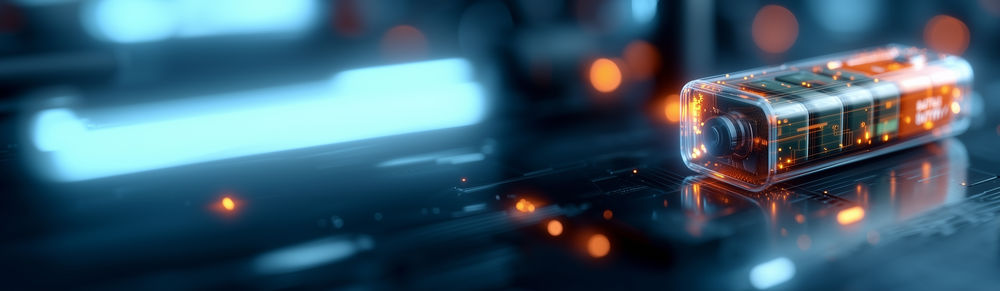
Topic World Battery Technology
The topic world Battery Technology combines relevant knowledge in a unique way. Here you will find everything about suppliers and their products, webinars, white papers, catalogs and brochures.