How glass learns to illuminate itself and create heat
Among other things, this can be used to produce electrically conductive and self-heating glass microreactors for the chemical and pharmaceutical industries
Advertisement
glass objects which glow in the dark, glass containers that heat up and cool down, or glass control knobs and switches that eliminate viruses and bacteria by themselves – all this seems to completely contradict our everyday experience of what glass can do. And yet, it is now within reach. To create such functionalized and precision-molded glasses, research teams at Fraunhofer IKTS in Dresden have transferred their experience with ceramic processes to glass manufacturing.
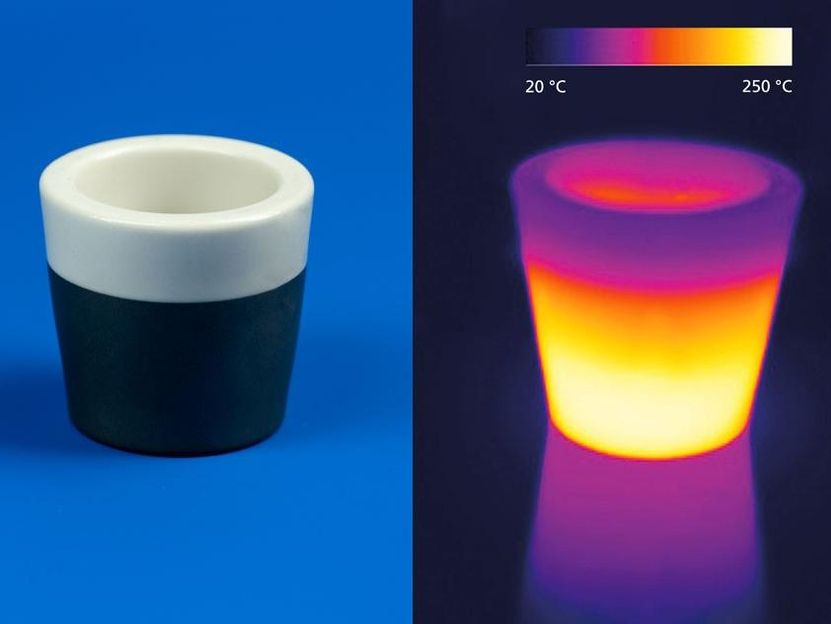
By combining glass powder and graphite, electri-cally conductive and self-heating microreactors or crucibles can be realized for the chemical and pharmaceutical industries.
© Fraunhofer IKTS
Thanks to the new shaping possibilities, glass can be processed at significantly lower temperatures and thus be mixed with fillers that enable new functions. This opens up a wide range of new fields of application in aerospace, safety engineering, vehicle construction or laboratory technology, for which glass was previously hardly an option. Depending on the process used, very different and complex shapes and properties are now possible that were previously either not feasible at all or required costly and sometimes environmentally harmful post-processing steps. These include a wide range of colors, but also metal-free, electrically conductive, heating, antibacterial and luminescent glasses. In addition, the IKTS glass shaping approaches in many cases reduce the consumption of energy, working time and other resources in glass component manufacturing.
Glass looks more valuable and has the “cool touch”
“This opens up new perspectives for this material,” emphasizes IKTS department head Dr. Tassilo Moritz. For example, glass has the potential to limit the massive use of plastic for many small everyday objects in favor of sustainable solutions: if glass can be colored, shaped, and functionalized almost at will, the plastic knobs in buses, trams or elevators, for example, could be replaced by control elements made of glass. The same would apply to furniture handles and knobs in daycare centers, retirement homes or hospitals. “Glass is still somewhat more expensive than plastic,” admits IKTS group leader Dr. Jochen Schilm. “But on the other hand, it is more durable and more hygienic. Glass does not become brittle and scratch as easily, and it also withstands chemical influences and UV radiation better.” There is also the design aspect: “Glass simply looks and feels better.”
Background: Although mankind has been producing and processing glass for an estimated 3500 years, in the past certain weaknesses of established glass technologies could never be fully overcome. For example, only parts with rounded edges can be produced from molten glass. When precise and sharp-edged shapes are required, the material needs costly regrinding. To create microstructures, as required in laboratory technology, for example, glass manufacturers must often resort to etching processes using dangerous and environmentally harmful hydrofluoric acid. Furthermore, it is very difficult to drill holes in classic glass.
Addition of graphite makes glass conductive
To overcome such limitations, the Fraunhofer engineers in Dresden have adapted several technologies that were previously typical for ceramics and plastics. One example: they add graphite to a glass powder. Recycled glass can also be used here as a contribution to the circular economy. From this glass-graphite powder mixture, a so-called feedstock is created, which is then injected into a shaping tool in an injection molding machine that produces precise geometries and microstructures. Among other things, this can be used to produce electrically conductive and self-heating glass microreactors for the chemical and pharmaceutical industries.
Glass powder can also be combined with color pigments or phosphorescent particles. This results in luminescent glass components that, for example, can still mark escape routes in dark environments even after a power failure, illuminate the hands and displays of watches or vehicle and aircraft fittings, or simply give jewelry a chic shimmer.
3D-printing for glass micromixer
The IKTS experts use industrial additive manufacturing technologies for particularly complex components such as micromixers. This can be, for example, the so-called vat photopolymerization process, in which the glass powder is stirred into a light-curable plastic and, after building up layer by layer to form a component, is cured with blue light, comparable to a filling at the dentist. Another additive printing process is “multi material jetting”. Here, the system deposits a liquid wax filled with glass particles in tiny droplets.
Since the unfinished, or “green”, body produced by these processes shrinks during subsequent sintering, as is familiar from ceramic components, a great deal of expertise is required to achieve exactly the projected component dimensions in the end. “For something like this, you need a very precise sintering regime,” says Dr. Jochen Schilm. And this is where the researchers at Fraunhofer IKTS have a special expertise: over decades, they have gained a great deal of experience with sintering processes and functionalization in ceramics, which they have now also transferred to the material glass.