A new process for the production of hydrogen with a low carbon monoxide content
fuel cells are on their way. But their use for apllications such as in vehicles will only become widespread when the expensive process of "refueling" with hydrogen can be made unnecessary. Transportable hydrogen sources are thus under investigation. The problem with this is that hydrogen produced by the usual processes contains rather large amounts of carbon monoxide (CO), which has a negative effect on the efficiency of fuel cells and can only be removed through multiple expensive production steps. James A. Dumesic and Rupali R. Davda at the University of Wisconsin have now developed a process that allows for the production of hydrogen with a low CO content.
The researchers are not using steam reforming of petroleum products, but rather of oxygen-containing compounds that can be derived from biomass, such as carbohydrates. Ethylene glycol is a simple molecule in this class of reactants and acts as the starting material. In a catalytic reforming process under pressure and at about 225 °C, these molecules in liquid water are split into hydrogen and carbon monoxide. In a second reaction, called the water-gas shift, the CO and water are then converted to CO2 and more hydrogen. Because both reactions occur in the same, relatively low, temperature range, they can be carried out together in the same reactor, which is especially advantageous for transportable hydrogen sources.
In the reforming process, CO and hydrogen are produced as gases, which form bubbles within the liquid phase. The water-gas shift occurs within these bubbles. It is an equilibrium reaction, which means that the reactants are not completely converted to products; instead, there is always a certain ratio of one to the other. In order to minimize the amount of CO, the conditions within the bubble have to be set so as to push the equilibrium as far as possible toward the product side. This can be achieved by maximizing the amount of water vapor in the bubbles. However, under these conditions, the starting materials for the reforming process can decompose. Davda and Dumesic found a trick to get around this problem: they divided the reactor into two areas. The reforming process takes place in the lower area, resulting in gas bubbles with relatively little water vapor. These then rise into the upper area, where the temperature is raised by about 10 °C. This causes a large amount of water to vaporize, so that the water-gas shift occurs under optimal conditions, bringing the CO content down to a level tolerable in fuel cells.
Most read news
Other news from the department science
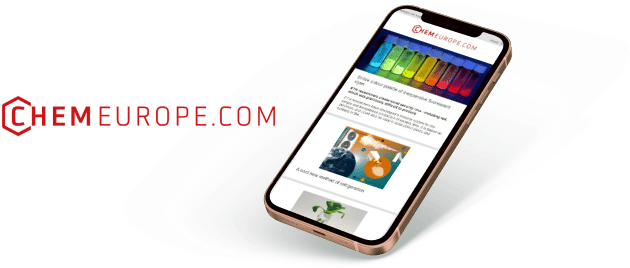
Get the chemical industry in your inbox
By submitting this form you agree that LUMITOS AG will send you the newsletter(s) selected above by email. Your data will not be passed on to third parties. Your data will be stored and processed in accordance with our data protection regulations. LUMITOS may contact you by email for the purpose of advertising or market and opinion surveys. You can revoke your consent at any time without giving reasons to LUMITOS AG, Ernst-Augustin-Str. 2, 12489 Berlin, Germany or by e-mail at revoke@lumitos.com with effect for the future. In addition, each email contains a link to unsubscribe from the corresponding newsletter.