LLNL teams with Quantum Fuel Systems to accelerate development of hydrogen storage technologies
Lawrence Livermore National Laboratory is working with Quantum Fuel Systems Technologies on a next-generation manufacturing technique for hydrogen storage vessels. As part of a $5.6 million three-year contract with the U.S. Department of Energy, Livermore researchers will demonstrate a unique high-speed composite processing technique.
LLNL participates in DOE's "National Hydrogen Storage Project," which is focused on developing material-based options that can operate at more practical temperatures and pressures and meet the stringent targets required for the ultimate commercialization of hydrogen vehicles across all platforms.
Hydrogen pressure vessels are typically made by winding carbon fiber wetted in adhesive around a liner made of either plastic or metal. This "wet winding" process is slow because the winding speed is limited by diffusion processes that control the adhesion of subsequent layers of fiber. Slow winding increases the cost of the pressure vessels because it requires continuous operation of a dedicated, expensive machine. Oven curing of the finished vessel is often required.
LLNL has developed a dry tape winding process that considerably reduces the time required for pressure vessel winding (15 minutes vs. 3 hours for wet winding), and does not require oven curing.
"This minimizes the cost of pressure vessel manufacturing," said Salvador Aceves, leader of LLNL's Energy Conversion and Storage Group.
"This technique can be applied to any kind of pressure vessel, including those used in the aircraft industry," said Andrew Weisberg, a composite materials engineer at LLNL.
Other news from the department research and development
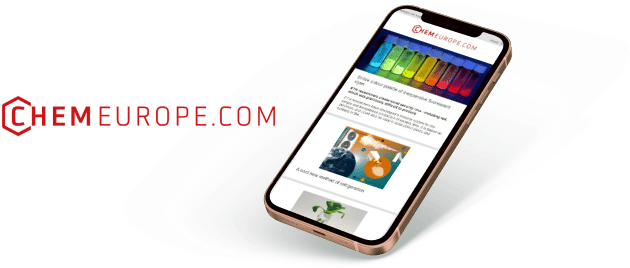
Get the chemical industry in your inbox
By submitting this form you agree that LUMITOS AG will send you the newsletter(s) selected above by email. Your data will not be passed on to third parties. Your data will be stored and processed in accordance with our data protection regulations. LUMITOS may contact you by email for the purpose of advertising or market and opinion surveys. You can revoke your consent at any time without giving reasons to LUMITOS AG, Ernst-Augustin-Str. 2, 12489 Berlin, Germany or by e-mail at revoke@lumitos.com with effect for the future. In addition, each email contains a link to unsubscribe from the corresponding newsletter.
Most read news
More news from our other portals
Last viewed contents
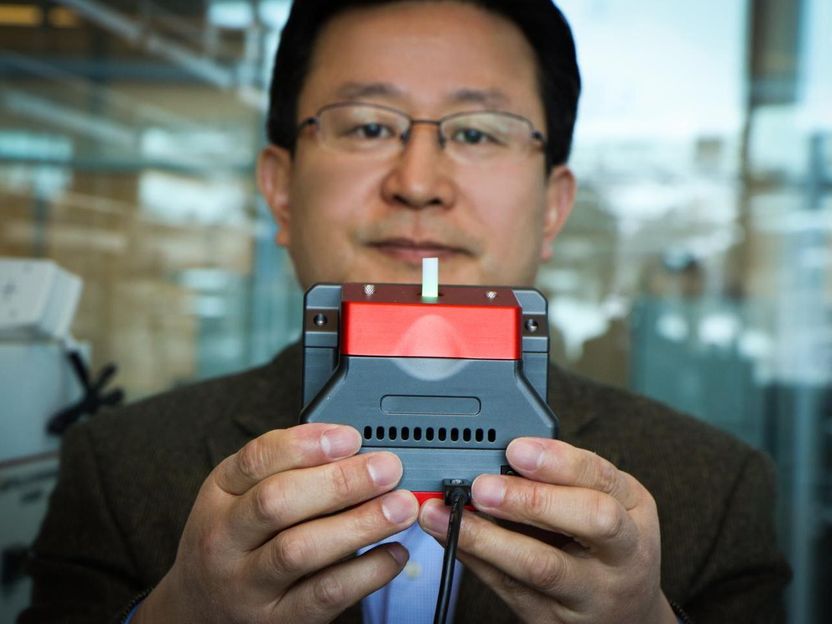
Sniffing out a dangerous vapor
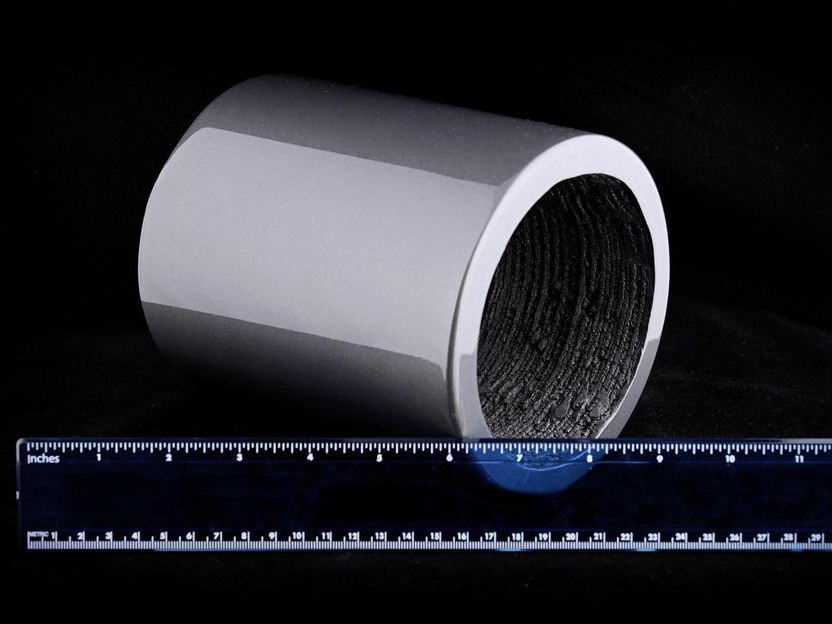
3-D-printed permanent magnets outperform conventional versions, conserve rare materials
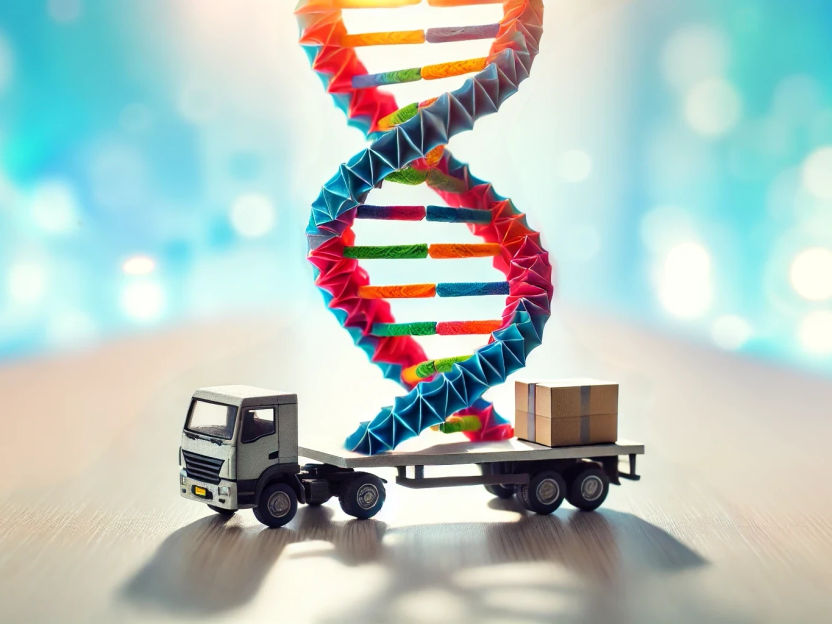