Putting climate-positive business ideas into practice
Start-ups made carbon-neutral fuels and turning carbon dioxide into stone
More and more ETH Zurich researchers are taking the plunge into entrepreneurship. By launching spin-offs, they hope to turn their lab findings into solutions that can help stem the rise in atmospheric carbon dioxide.
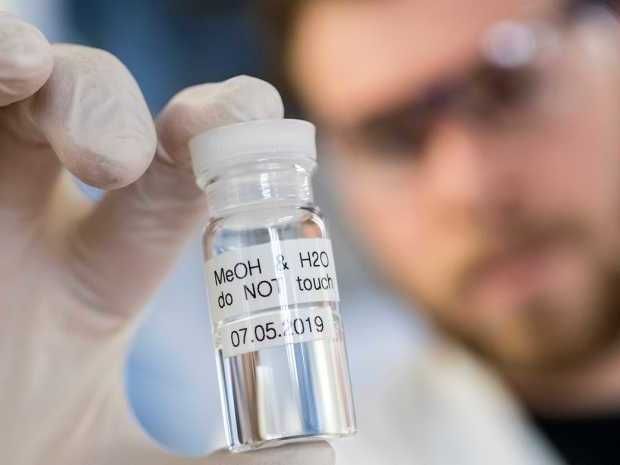
Using solar technology, the spin-off Synhelion produces a CO2-neutral fuel.
ETH Zürich
There is no shortage of evidence for what the Fifth Assessment Report of the Intergovernmental Panel on Climate Change (IPCC) describes as an “unequivocal warming of the climate system”. At no point in the past 800,000 years has the concentration of greenhouse gases in the atmosphere been as high as it is today. Since 1750, human activity has caused 555 billion tonnes of carbon dioxide to be released into the atmosphere, raising the concentration of carbon dioxide by 40 percent above pre-industrial levels. Between 1880 and 2012, the average temperature of the Earth’s surface rose by 0.85 degrees Celsius. And with global snow and ice cover steadily shrinking, sea levels are rising by an average of 3 millimetres a year.
Scientists are united in their belief that humanity must do everything in its power to slow the rise in the concentration of greenhouse gases in the atmosphere, or even reverse it. There has been a noticeable increase in efforts by ETH Zurich researchers to come up with potential solutions for climate change. And increasing numbers of them are also venturing beyond the walls of academia and striving to put climate-positive business ideas into practice. Of the 242 spin-offs established at ETH Zurich since 2010, 34 are pursuing ways to combat global warming. In this article, we take a closer look at two examples: one from the energy sector, the other from the construction industry.
Carbon-neutral fuels made from sunlight and air
Since its founding in 2016, Synhelion has been working on something that sounds almost too good to be true: a solar technology that can reverse the combustion process. The company’s mission is to produce synthetic liquid fuels exclusively from sunlight and air. Known as solar fuels, these release only as much CO2 during combustion as was previously extracted from the air in order to produce them, thereby giving them the potential to make the transport industry practically carbon-neutral. Taken as a whole, air, sea and road transport currently release some eight billion tonnes of carbon dioxide into the atmosphere, making it responsible for a quarter of anthropogenic CO2 emissions.
“We believe that liquid solar fuels have an important role to play in the energy transition,” says Gianluca Ambrosetti, CEO of Synhelion. He rightly points out that no other energy carrier comes close to matching the energy density and long-term storage capabilities of liquid fuels. “What’s more, our solar fuels are a drop-in technology, which means they don’t require any additional infrastructure,” says Ambrosetti. “They can be processed in existing refineries and distributed via the network of filling stations that is already in place.”
Highly concentrated solar radiation
Synhelion’s ingenious solar technology is based on three innovations originally developed by a group of researchers led by Aldo Steinfeld, Professor of Renewable Energy Carriers at ETH Zurich. Synhelion is now seeking to take these innovations to the next level. The first is the solar receiver, a black chamber containing a greenhouse gas. Solar radiation – concentrated several thousand times by mirrors – shines through the quartz glass window that fronts this chamber and heats up the gas to well over 1,000 degrees Celsius. The second innovation is the ceramic foam technology used in the thermochemical reactor. When heated to a sufficient temperature by the hot gas, this reactor is able to split water and carbon dioxide to produce syngas, a mixture of hydrogen and carbon monoxide. Conventional methods can then be used to convert this syngas into liquid fuels such as methanol, gasoline and kerosene. The third innovation is a thermal energy-storage system that can be used to drive the reactor processes at night and on overcast days.
A year and a half have passed since Steinfeld and his team set up a mini-refinery, which produces around one decilitre of methanol a day, on the roof of the Machine Laboratory building at ETH Zurich. “This pilot plant proves that we can make sustainable fuel from sunlight and air under real-life conditions,” says Steinfeld.
The next goal, says Ambrosetti, is to scale up the processes, increase the efficiency and drive down costs. Ambrosetti acknowledges that people may have doubts about scalability: “I think it will be at least five more years before we can start using this technology on an industrial scale.” That’s why Synhelion is developing an interim solution, known as solar upgrading, to shorten the time to market. “By adding methane to the mixture of water vapour and carbon dioxide gas, the temperature required for thermochemical conversion into syngas can be reduced to as little as 800 degrees Celsius,” says Ambrosetti. “This simplifies the whole process, which means it should only take us two more years to get to the point where we can produce affordable solar fuels that release half the net CO2 emissions of fossil fuels.”
Turning carbon dioxide into stone
Neustark – an ETH spin-off founded in 2019 – is pursuing a business model based on an entirely different concept. The company is developing a technology that turns carbon dioxide into stone by binding it with concrete aggregate, thereby transforming it into high-grade limestone. The benefits include both an upgraded aggregate and long-term carbon storage. “The construction industry has so far made little progress in reducing emissions – and that’s because so much research just gets filed away and never used,” says Johannes Tiefenthaler, one of the spin-off’s two founders. “I would like to see the effort that I’m putting into my doctorate make a tangible difference somewhere.”
As part of his Master’s degree, Tiefenthaler was already investigating various ways of converting carbon dioxide into limestone by reacting it with minerals. There are enough minerals on Earth to bind hundreds of billions of tonnes of carbon dioxide. However, as Tiefenthaler explains, many of them – such as magnesium silicate – are not particularly reactive, so they must first be heated to 700 degrees Celsius. In contrast, demolition rubble broken into concrete aggregate has proven to be highly reactive due to the huge total surface area of the numerous particles, each just a few millimetres in size. As a result, the concrete aggregate forms very stable chemical compounds with carbon dioxide, without the need for any pre-treatment.
“What I love about this solution is that it’s ready to go now, not just in five or ten years,” says economist Valentin Gutknecht, Neustark’s second founder. The main challenge right now, he says, is juggling all the different issues involved. “As well as ensuring the properties of the concrete are exactly right, we also have to navigate the convoluted web of CO2 certification.”
Negative CO2 emissions offer economic benefits
While Tiefenthaler works at the Department of Mechanical and Process Engineering to deliver the next generation of technology for the mineralisation of carbon dioxide, Gutknecht and an ever-growing team of employees are busy focusing on the operational side of the business. As part of a project funded by the Federal Office for the Environment and the Swiss Climate Foundation, Neustark has set up a pilot plant at the Kästli concrete works in Rubigen near Bern. Part of this pilot plant is a bright orange, skip-like container, in which liquid CO2 is added to rubble from demolished concrete structures. After soaking in the bath of carbon dioxide for around two hours, the pieces of concrete rubble may still look the same, but they weigh significantly more because the tiny pores in the rough surface of the concrete have absorbed approximately 10 kilograms of CO2 per cubic metre.
The carbon dioxide forms a chemical bond with the calcium oxide in the concrete rubble. This produces limestone crystals, which significantly enhance the qualities of the concrete aggregate: by using this recycled, upgraded aggregate to make fresh concrete, the same strength and rigidity can be achieved with less cement. Concrete production worldwide releases over 2 billion tonnes of carbon dioxide into the air each year. This represents around 7 percent of anthropogenic CO2 emissions. By cutting the amount of cement required in construction, Neustark’s technology can help reduce the industry’s carbon footprint by eliminating some of the emissions that would otherwise occur during the production of cement.
But Gutknecht and Tiefenthaler are quick to point out another important advantage: thanks to their ingenious method of capturing carbon dioxide from the air, soaking it into the pores of the concrete aggregate and binding it permanently into limestone, they can even reverse CO2 emissions. “There are very few technical concepts that deliver genuine negative emissions,” says Tiefenthaler. Use of these concepts has so far been limited due to a lack of effective incentive schemes and business models. “This is where our method is unique, because it shows how binding carbon dioxide can create added value. The enhanced qualities of the concrete aggregate prove that negative emissions don’t have to raise costs, but can actually provide economic benefits,” says Gutknecht.
Other news from the department science
Most read news
More news from our other portals
Something is happening in the chemical industry ...
This is what true pioneering spirit looks like: Plenty of innovative start-ups are bringing fresh ideas, lifeblood and entrepreneurial spirit to change tomorrow's world for the better. Immerse yourself in the world of these young companies and take the opportunity to get in touch with the founders.