High-tech lubricant forms by itself when needed
Precisely where friction is high, lubricants are created that ensure lower friction: At the Vienna University of Technology, this was achieved with special 2D materials
Advertisement
Our bodies have a few things in common with machines: We have moving joints, friction and wear occur, so you need suitable lubricants. The body produces them naturally all by itself - something similar is now possible with machines.
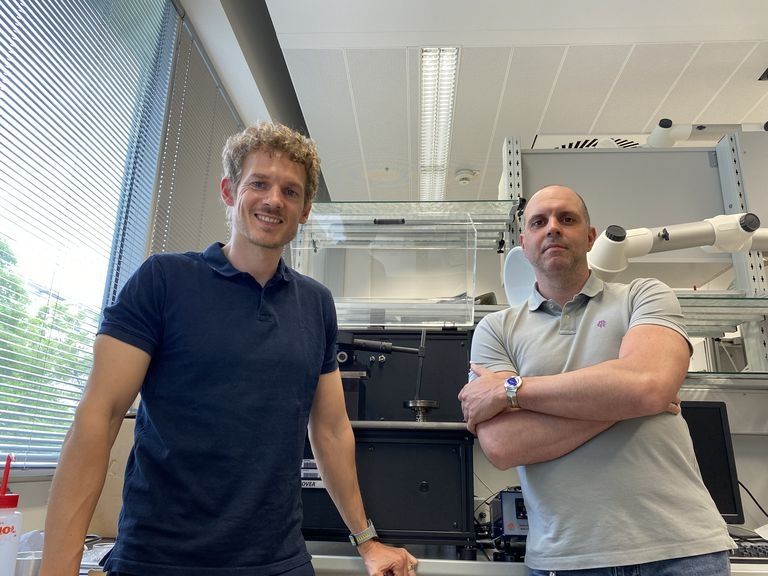
Philipp Grützmacher and Carsten Gachot in front of a tribometer
Technische Universität Wien
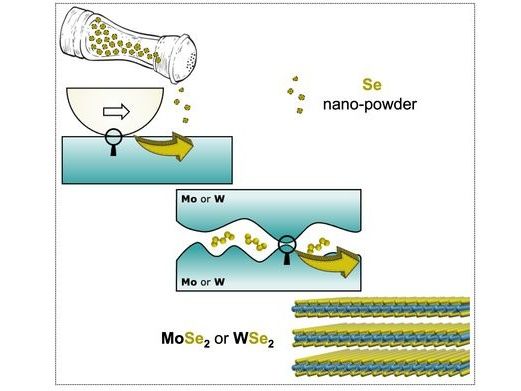
In the form of nanoparticles, selenium is applied to the molybdenum surface - molybdenum diselenide is then formed under heavy loading.
Technische Universität Wien
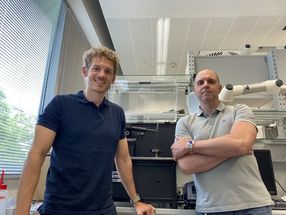
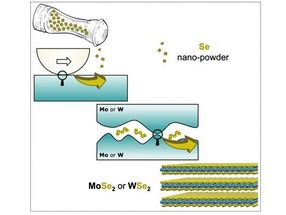
By choosing suitable materials, it is possible to achieve that special 2D materials form under mechanical stress, which are highly effective in reducing friction - high friction thus leads to a reduction in friction all by itself, the system regulates itself. Especially for applications in space, where liquid lubricants fail and no maintenance is possible, this new technology holds great advantages.
Thin layers that glide over each other
Tribology, the science of friction and wear, has for years been intensively studying so-called 2D materials - particles consisting of only one or a few atomic layers. This class of materials includes, for example, molybdenum disulfide or molybdenum diselenide - in the middle there is a layer of molybdenum atoms, with sulfur or selenium atoms coupled above and below.
"Such ultrathin platelets can slide over each other with very little resistance," says Dr. Philipp Grützmacher of the Institute of Engineering Design and Product Development at TU Wien. "Therefore, these materials are an excellent lubricant." Philipp Grützmacher conducts research as part of the team led by Prof. Carsten Gachot, who heads the Tribology Research Department at TU Wien.
Unlike conventional lubricants such as oil, which are used in a liquid state, 2D materials can be used in powder form. This is a major advantage, especially when a machine needs to function at high temperatures or in a vacuum, where liquids would quickly evaporate. "That's why such lubricants play a particularly important role in space technology; they were used, for example, in the James Webb Space Telescope," says Carsten Gachot.
Under ordinary conditions on Earth, however, such materials are difficult to handle. Indeed, contact with oxygen or atmospheric humidity can oxidize them, rendering them unusable. "The optimal solution is therefore a 2D material that is first created exactly where it is needed," says Philipp Grützmacher. "And that is exactly what we have now developed."
Friction creates lubricant
To do this, one simply takes a mechanical component made of steel and coats it with a layer of molybdenum a few micrometers thick. Selenium is then added in powder form. "When mechanical stress is applied, such as when two such components rub against each other, a tribochemical reaction occurs, selenium and molybdenum combine to form molybdenum diselenide flakes, which then act as a lubricant," Grützmacher explains. "Our measurements show that as soon as strong friction occurs, the lubricant is produced, the friction immediately decreases dramatically and continues to decrease throughout the experiment." Using special imaging techniques, it was possible to demonstrate that this effect actually results from the formation of ultrathin molybdenum selenide layers.
Unlike coatings made of 2D materials synthesized in advance (e.g., MoS2), the starting materials (molybdenum and selenium powder) for the process do not decompose in contact with oxygen or atmospheric moisture. This significantly expands the application range of this lubricant system. This technology is not only interesting for space applications, but also for many areas of application in which liquid lubricants cause problems - for example, because high temperatures occur, because the process is to take place in a vacuum, or because contamination could occur when oils are used.
Another important advantage is that the lubricant is always formed exactly where it is needed, which can also be repeated at any time by simply adding powder. Thus, a significantly more efficient lubricant system with a longer service life has been created.
Note: This article has been translated using a computer system without human intervention. LUMITOS offers these automatic translations to present a wider range of current news. Since this article has been translated with automatic translation, it is possible that it contains errors in vocabulary, syntax or grammar. The original article in German can be found here.