Producing carboxylic acids employing an environmentally friendly technique
Electrochemistry provides new opportunities
Researchers at Mainz University and Evonik have developed an innovative method to cleave and oxidize double- and triple-bonds in hydrocarbon.
Polyamides are present in many different products, such as ropes for mountaineering, parachutes of nylon, and materials for 3D printing. Dicarboxylic acids are used as chemical building blocks for these polyamides. However, their production has been challenging to date because current methods of generating dicarboxylic acids from saturated or unsaturated hydrocarbons frequently involve multiple steps as well as the use of heavy metals and strong acids, while the related energy consumption and costs are extensive. Furthermore, the process often results in the release of nitrogen oxides (NOx), which are among the most problematic greenhouse gases as far as the climate is concerned. Researchers at Johannes Gutenberg University Mainz (JGU) and Evonik have recently developed an environmentally friendly way to produce (di)carboxylic acids. They report on this in a paper recently published in Nature Communications.
Electrochemistry provides new opportunities
"Our technique is the first-ever process to make the building blocks for polyamides from petrochemical compounds and even unsaturated fatty acids using a fairly sparing approach," said Professor Siegfried Waldvogel, speaker of the SusInnoScience – Sustainable Chemistry as the Key to Innovation in Resource-efficient Science in the Anthropocene – research focus at Mainz University. The new technique involves an electrochemical method in which hydrocarbons with double or triple bonds are transferred to an electrolysis cell filled with a solvent. Oxygen is then added, whereby the greater the oxygen concentration, the more efficient the process.
"What is really fascinating about our process is that the electrochemical intervention is needed at both the anode and the cathode," explained Waldvogel. While oxidative radicals are created at the anode, the oxygen at the opposite electrode is reduced to superoxide anions. The radicals and the superoxide anions come together in the solution and react to form the desired product, carboxylic acid. The researchers have repeated the process successfully in both standard and flow electrolytic cells.
Process requires only oxygen, electricity, and hydrocarbon compounds
This new technique has many advantages: Heavy metals and strong acids are no longer necessary while no nitrogen oxides are generated. The only starting materials needed are oxygen, electricity, and hydrocarbons with double bonds. Because no byproducts are created and the solvent can be recovered and recycled, the process is very cost-effective. "This is an innovative and less detrimental process for producing carboxylic acids, thus providing a valuable contribution to those manufacturers who wish to replace the climate-damaging processes with a green approach," concluded Waldvogel. The research team is currently working on a scale-up of the lab process to make it practicable for commercial use.
Original publication
Original publication
J. Nikl et al., Electrochemical oxo-functionalization of cyclic alkanes and alkenes using nitrate and oxygen, Nature Communications, 28. Juli 2023
Topics
Organizations
Other news from the department science
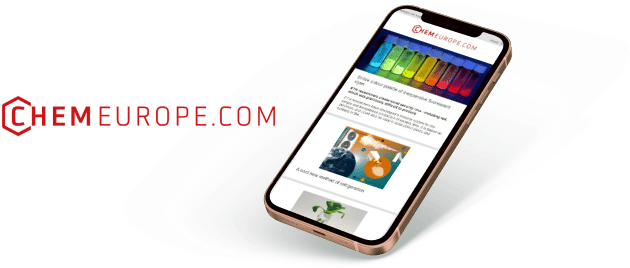
Get the chemical industry in your inbox
By submitting this form you agree that LUMITOS AG will send you the newsletter(s) selected above by email. Your data will not be passed on to third parties. Your data will be stored and processed in accordance with our data protection regulations. LUMITOS may contact you by email for the purpose of advertising or market and opinion surveys. You can revoke your consent at any time without giving reasons to LUMITOS AG, Ernst-Augustin-Str. 2, 12489 Berlin, Germany or by e-mail at revoke@lumitos.com with effect for the future. In addition, each email contains a link to unsubscribe from the corresponding newsletter.
Most read news
More news from our other portals
Last viewed contents
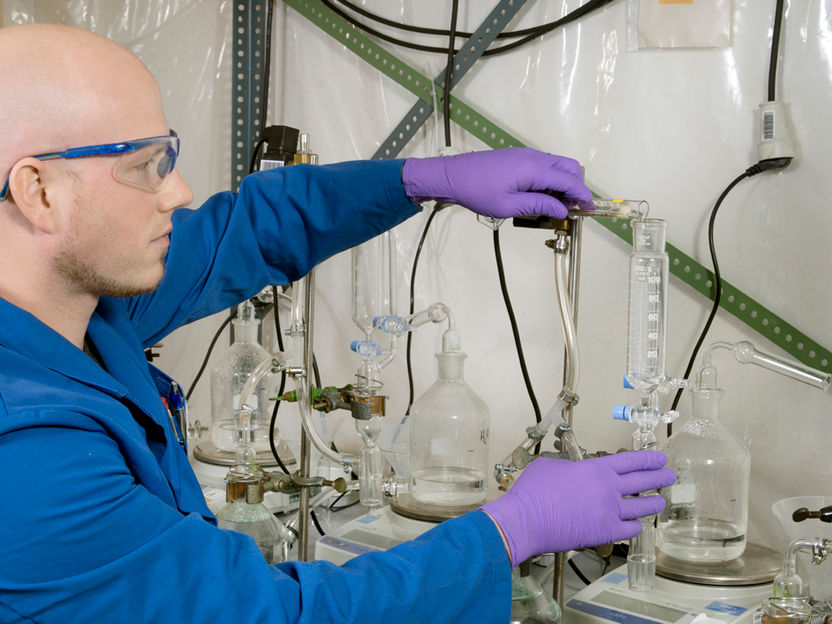
How good is the measurement method? - Three more interlaboratory tests on safety of chemicals
Dogliotti's_principle
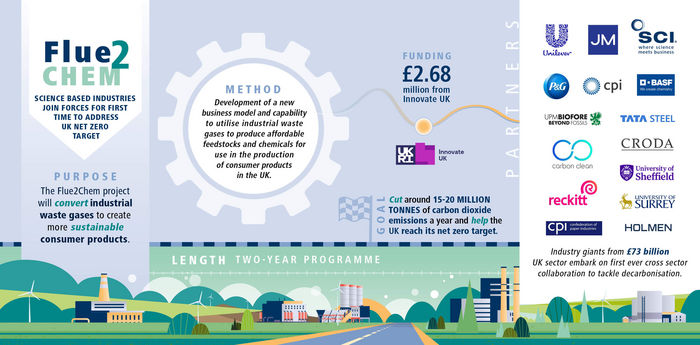