Researchers discover smarter way to recycle polyurethane
Researchers at Aarhus University have found a better method to recycle polyurethane foam
Advertisement
Polyurethane (PUR) is an indispensable plastic material used in mattresses, insulation in refrigerators and buildings, shoes, cars, airplanes, wind turbine blades, cables, and much more. It could be called a wonder material if it weren’t also an environmental and climate burden. Most of the PUR products discarded worldwide end up being incinerated or dumped in landfills.
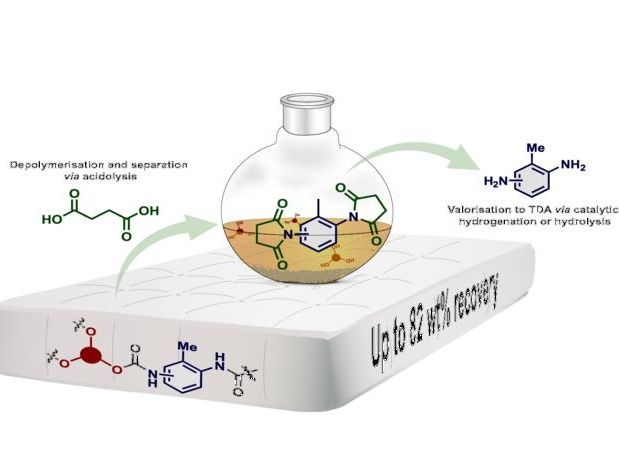
The graphic shows how the new combination of acidolysis and hydrolysis can recover up to 82 weight percent of the original material from flexible PUR foam – used in mattresses – as two separate fractions of diamines and polyols. The diamine is shown as TDA (toluene diamine).
Thomas Balle Bech, Aarhus University
This is problematic because the main components of the material are primarily extracted from fossil oil. And we’re talking about significant quantities. In 2022, the global market for PUR reached almost 26 million tons, and a forecast for 2030 predicts nearly 31.3 million tons, with about 60% being foam in various forms.
However, there is a small but growing industry that chemically breaks down (depolymerizes) PUR into its original main components, polyol and isocyanate, with the aim of reusing them as raw materials in new PUR products.
Still, there is a long way to go before their output can actually compete with “virgin” materials. It is expensive to separate and purify the desired elements.
Breaking down and separating in one go
This is where a research team from Aarhus University comes in with a smart idea. They base their method on what the companies in question already use, namely breaking down PUR foam with acid (acidolysis).
But the companies do not separate the broken-down PUR into polyol and isocyanate. This results in a mixture that cannot be directly recycled but requires their customers to use new recipes.
The AU researchers are not only able to break down PUR and separate the two main components – they can do it in one go. They heat flexible PUR foam to 220°C in a reactor with a bit of succinic acid (see fact box). Afterwards, they use a filter that catches one material and lets the other pass through.
It is the polyols that pass through, and they do so in a quality comparable to virgin polyol, making it possible to use them in new production of polyurethane. The solid part of the product mixture that is filtered out is transformed into a so-called diamine in a simple hydrolysis process, which is used in the production of isocyanates and thus PUR.
In this way, the researchers are able to recover up to 82 weight percent of the original material from flexible PUR foam – used in mattresses – as two separate fractions of diamines and polyols. The researchers have recently published their findings in the scientific journal Green Chemistry.
Enormous potential in the industry
"The method is easy to scale up," points out one of the study’s authors, Steffan Kvist Kristensen, assistant professor at the Interdisciplinary Nanoscience Center (iNANO) at Aarhus University.
He sees enormous potential for recycling the PUR foam waste at the factories that use it as raw material (slabstock) in their production.
"But the prospect of also handling PUR waste from consumers requires further development," he adds.
... but still a long way to go to a circular economy
Manufacturers in the PUR industry each use unique formulae to achieve specific material properties for their products.
Therefore, a number of challenges need to be solved before a real economy in recycling polyurethane can be achieved:
- Waste sorting
- Logistics
- Sorting PUR into types
Depolymerization is thus only a small part of the solution.