Stronger and safer: new design strategy for aluminium combines strength with hydrogen embrittlement resistance
40% increase in strength and a five-fold improvement in hydrogen embrittlement resistance compared to scandium-free alloys
aluminium alloys are well-known for their low weight and corrosion resistance, making them ideal candidates for applications in a low-carbon economy - from lightweight automobiles to tanks for storing green hydrogen. However, their widespread application is limited by a key challenge: they suffer from embrittlement leading to cracking and failure when exposed to hydrogen. Till now, alloys resistant to hydrogen embrittlement were rather soft, limiting their application in hydrogen-related technologies that require high strength. Now, researchers from the Max Planck Institute for Sustainable Materials (MPI-SusMat) in Germany, together with partners from China and Japan, have developed a new alloy design strategy that overcomes this dilemma. Their approach enables both exceptional strength and superior resistance to hydrogen embrittlement (HE), paving the way for safer and more efficient aluminium components in the hydrogen economy. They have published their results in the journal Nature.
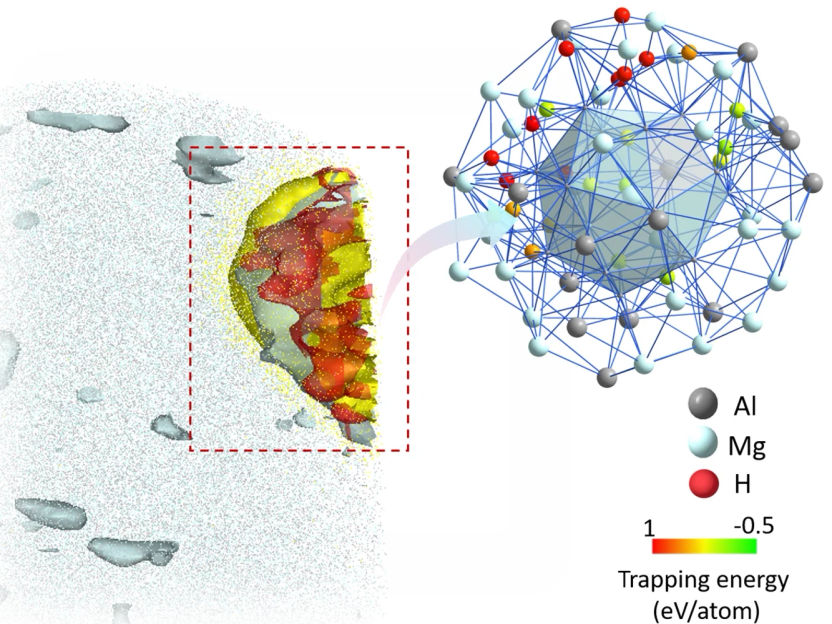
Complex nanoprecipitates are able to trap hydrogen inside aluminium alloys while maintaining their strength.
© Nature 2025; DOI:10.1038/S41586-025-08879-2
Dual nanoprecipitates trap hydrogen and boost strength
At the heart of the breakthrough is a complex, size-sieved precipitation strategy in scandium-added aluminium-magnesium alloys. Through a two-step heat treatment, the researchers engineered fine Al3Sc nanoprecipitates on which a shell of a highly structurally complex Al3(Mg,Sc)2 forms in-situ. These dual nanoprecipitates are distributed throughout the alloy to serve two key roles: the Al3(Mg,Sc)2 phase traps hydrogen and enhances HE resistance, while the fine Al3Sc particles boost strength.
"Our new design strategy solves this typical trade-off. We no longer have to choose between high strength and hydrogen resistance - this alloy delivers both," Professor Baptiste Gault, head of the group “Atom Probe Tomography” at MPI-SusMat and one of the corresponding authors of the newly published work.
The results are compelling: a 40% increase in strength and a five-fold improvement in hydrogen embrittlement resistance compared to scandium-free alloys. The material even achieves a record uniform tensile elongation in hydrogen-charged aluminium alloys of up to 7 ppmw - an indicator of excellent ductility under hydrogen exposure. Atom probe tomography measurements carried out at MPI-SusMat were essential in verifying the role of the Al3(Mg,Sc)2 phase in hydrogen trapping at the atomic level, offering insights into how the alloy design works on a fundamental scale. Experiments carried out at the partner institutes included electron microscopy and simulation.
From lab to industry
The researchers tested their approach across various Al alloy systems, and also demonstrated scalability by using water-cooled copper mould casting and thermomechanical processing methods that align with current industrial standards. This research lays the groundwork for a new generation of aluminium materials tailored for the demands of a hydrogen-powered future - safe, strong, and ready for industrial use.
This work was jointly carried out mainly by researchers from the Xi’an Jiaotong University (China), the Shanghai Jiao Tong University (China) and at the Max Planck Institute for Sustainable Materials (Germany).
To the point
- New alloy design for aluminium: Researchers developed a dual nanoprecipitate strategy combining Al3Sc and Al3(Mg,Sc)2 phases, achieving a 40% increase in strength and a five times higher resistance to hydrogen embrittlement compared to Sc-free alloys, without sacrificing ductility.
- Tuning the microstructure: An Al3(Mg,Sc)2 phase traps hydrogen and enhances hydrogen embrittlement resistance, while fine Al3Sc particles boost strength.
- Scalable innovation: The design was successfully tested in near-industrial conditions, including copper mould casting and thermomechanical processing, showing clear potential for industrial-scale production.
Original publication
Shengyu Jiang, Yuantao Xu, Ruihong Wang, Xinren Chen, Chaoshuai Guan, Yong Peng, Fuzhu Liu, Mingxu Wang, Xu Liu, Shaoyou Zhang, Genqi Tian, Shenbao Jin, Huiyuan Wang, Hiroyuki Toda, Xuejun Jin, Gang Liu, Baptiste Gault, Jun Sun; "Structurally complex phase engineering enables hydrogen-tolerant Al alloys"; Nature, 2025-4-30