BASF installs first continuous production plant for Catamold
By 2002, BASF Aktiengesellschaft will have installed the world's first continuous production plant for Catamold® granules for use in powder injection molding, thus expanding the capacity for Catamold granules at the Ludwigshafen site by 1000 metric tons per year. The quality of the Catamold granules will be further improved by this continuous production process, which, for the customer, is an important step in the direction of "net shape production" (elimination of reworking), even in the case of highly complex powder injectionmolded parts. In this way, BASF is further consolidating its quality leadership. With double digit sales growth rates, BASF already now holds a 70% share of the European market, making it the leading supplier for powder injection molding, and the company also intends to boost its market growth in the United States and Asia. BASF's objective is to become the world's number one supplier of granules for powder injection molding.
In addition to the Catamold line, BASF also markets high quality, ultrafine carbonyl iron powders, an important alloy component in metal powder injection molding. Here, too, BASF has chalked up double digit sales growth rates in recent years.
BASF developed Catamold ten years ago, making it possible for the first time to carry out powder injection molding in continuous production plants. This greatly boosted the growth rate of the fledgling powder injection molding technology. Today, there are hardly any sectors that do not use Catamold. Important examples are mechanical engineering, automobiles, communications and electronics, medical and consumer goods.
Catamold products are injection ready granules consisting of metal or ceramic powders and a patented binder system. The special binder that BASF has developed specifically for powder injection molding technology allows debindering that is ten times faster than with conventional methods. This gentle debindering at low temperatures takes place in the solid state of all Catamold components, ensuring a high dimensional stability of the parts made in this manner. The use of Catamold products for powder injection molding translates into greater costeffectiveness for the customer.
The process of powder injection molding is ideal for the cost effective production of highly complex parts made of metal or ceramic powder such as, watch casings or automotive technology components in large quantities. In recent years, this market has grown by approximately 15% per year. BASF expects that this growth trend will continue and that the technology of powder injection molding will develop into the leading process for the production of highly complex parts.
Dr. Roland Spahl, head for powder injection molding operation worldwide, explains, "We are convinced of the success of powder injection molding technology and are promoting it by continuously improving the Catamold product line. Our comprehensive applications and technology consulting service supports our customers worldwide through the entire process chain, from the initial idea to the final product. Catamold customers can concentrate fully on their core business - the production and marketing of highly complex components."
Most read news
Other news from the department research and development
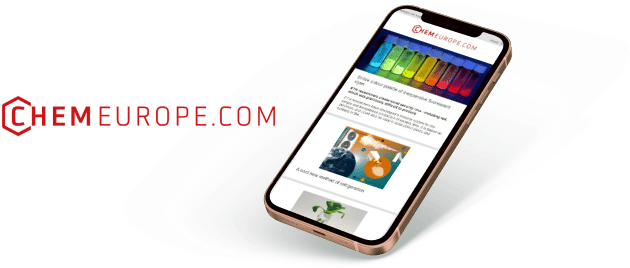
Get the chemical industry in your inbox
From now on, don't miss a thing: Our newsletter for the chemical industry, analytics, lab technology and process engineering brings you up to date every Tuesday and Thursday. The latest industry news, product highlights and innovations - compact and easy to understand in your inbox. Researched by us so you don't have to.