Materials research: Biocatalytic foams with enormous durability and activity
KIT Researchers Develop a New Class of Materials for Biocatalysis Processes from Enzymes
Industrial biocatalysis with enzymes is considered a "gamechanger" in the development of a sustainable chemical industry. With the help of enzymes, an impressive range of complex molecules such as active pharmaceutical ingredients can be synthesized under environmentally friendly conditions. Researchers at the Karlsruhe Institute of Technology (KIT) have now developed a new class of materials by producing enzymes as foams that have enormous durability and activity. A patent application has already been filed for the novel manufacturing process of the enzyme foams.
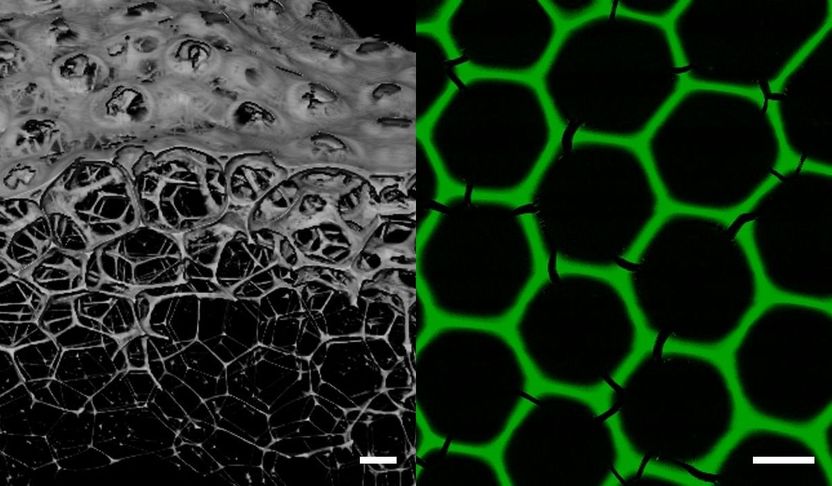
New biomaterials for industrial biocatalysis: enzyme foams form three-dimensional porous networks with stable hexagonal honeycomb structure.
Julian Hertel, KIT
Researchers are working intensively on new process technologies to further develop the field of industrial biocatalysis, which is mainly used in the production of pharmaceuticals and specialty chemicals. In biocatalysis, enzymes accelerate reactions instead of chemical catalysts, thus saving raw materials and energy. The aim now is to provide enzyme biocatalysts continuously and in large quantities under conditions that are as gentle as possible. To enable efficient material conversions, the enzymes are immobilized in microstructured flow reactors. They are spatially fixed and bound to a reaction-bearing material and thus have limited mobility, which leads to a higher concentration of enzymes and thus to higher productivity.
Foamed microdroplets from self-assembling enzymes
Normally, enzymes change their structure during foaming and thus lose their biocatalytic activity. However, the new protein foams have tremendous durability and activity. The activity is a measure of the effectiveness of the enzyme, which ensures that starting materials react with each other as quickly as possible. To make the protein foams, two dehydrogenase enzymes are mixed that carry matching linkage sites so they can spontaneously form a stable protein network. "A gas stream is then added to this mixture in a microfluidic chip so that microscopic bubbles of uniform size form in a controlled manner," says Professor Christof Niemeyer of the Institute of Biological Interfaces-1, explaining the process. The foam of uniform bubble size produced in this way is applied directly to plastic chips and dried, causing the proteins to polymerize and form a stable, hexagonal lattice.
"These are monodisperse "all-enzyme foams," three-dimensional, porous networks consisting exclusively of biocatalytically active proteins," says Niemeyer, characterizing the composition of the new materials. The stable hexagonal honeycomb structure of the foams has an average pore diameter of 160 µm and a lamella thickness of 8 µm and is formed from the freshly produced spherical bubbles of approximately the same size after a few minutes.
Efficient use of active and stable full enzyme foams
In order to use enzymes efficiently for material transformations, they must be immobilized in large quantities under the gentlest possible conditions to preserve their activity. Until now, enzymes have been immobilized on polymers or carrier particles, but this requires valuable reactor space and can compromise activity. "Compared to our previously developed "full enzyme hydrogels," the new foam-based materials create a significantly larger surface area where the desired reaction can take place," Niemeyer describes the major improvement. In contrast to theoretically expected results, the new foams surprisingly show strikingly high durability, mechanical resistance and catalytic activity of the enzymes, something that had not previously been achieved when foaming proteins.
The researchers assume that the stability is due to the matching linkage sites with which the enzymes are equipped. This allows them to self-assemble, forming a highly cross-linked lattice during drying that gives the new material unique stability. "Surprisingly, the newly developed enzyme foams are significantly more stable after drying for four weeks than the same enzymes without foams," Niemeyer explains the advantages, "This is of great interest for commercialization, as it greatly simplifies stock production and shipping."
The new biomaterials open up versatile avenues for innovation in industrial biotechnology, materials science or even food technology. For example, the protein foams could be used in biotechnological processes to produce valuable compounds more efficiently and sustainably. The research team was able to show that the foams can be used to produce the industrially valuable sugar tagatose, which is a promising alternative to refined sugar as a sweetener.
Note: This article has been translated using a computer system without human intervention. LUMITOS offers these automatic translations to present a wider range of current news. Since this article has been translated with automatic translation, it is possible that it contains errors in vocabulary, syntax or grammar. The original article in German can be found here.
Original publication
Julian S. Hertel, Patrick Bitterwolf, Sandra Kröll, Astrid Winterhalter, Annika J. Weber, Maximilian Grösche, Laurenz B. Walkowsky, Stefan Heißler, Matthias Schwotzer, Christof Wöll, Thomas van de Kamp, Marcus Zuber, Tilo Baumbach, Kersten S. Rabe, Christof M. Niemeyer: "Biocatalytic Foams from Microdroplet-Formulated Self-Assembling Enzymes."; Advanced Materials, 2023.