Metal encapsulation optimizes chemical reactions
The chemical industry consumes millions of tons of packing materials as catalytic support media or adsorbents in fixed-bed reactors and heat storage systems. Fraunhofer researchers have developed a means of encapsulating these filler particles in metal that multiplies their thermal conductivity by five.
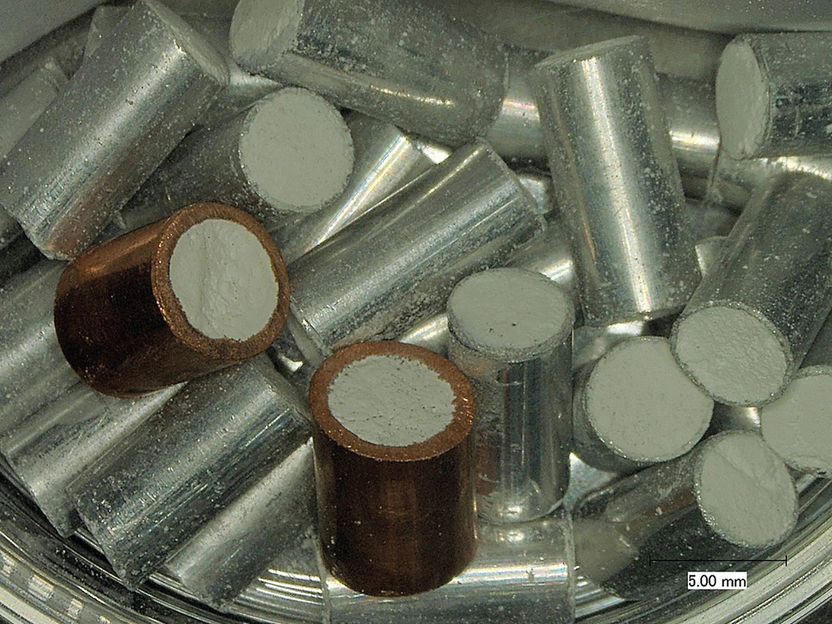
The chemical industry uses large quantities of packing materials. To protect the millimeter-scale particles against abrasion, Fraunhofer IKTS encapsulates them in a layer of metal that boosts their thermal conductivity by a factor of five.
© Fraunhofer IKTS
Random packing materials are used in many chemical reactors and heat storage systems as catalytic support media or adsorbents. Several million tons of these functional materials are consumed every year in industrial processes to produce chemical feedstock. To ensure that these processes produce the desired results, the packing materials have to be able to conduct heat efficiently. This is not always easy, because the gaps between the millimeter-scale particles prevent heat from being conducted optimally throughout the packed bed. Chemical companies therefore have to build special heatconducting structures into their reactors. “This is time-consuming and expensive,” says Jörg Adler, a researcher at the Fraunhofer Institute for Ceramic Technologies and Systems IKTS in Dresden. Together with colleagues at the Fraunhofer Institutes for Machine Tools and Forming Technology IWU in Chemnitz and for Interfacial Engineering and Biotechnology IGB in Stuttgart, Adler has developed a concept that increases the heat transfer capacity of the packing material fivefold. Their concept involves encapsulating cylindrical filler particles in metal. The points of contact between the metal-encapsulated particles form a metal framework that enables heat to be conducted throughout the packed bed faster and more efficiently.
Five times more efficient
The scientists have conducted tests in the laboratory that prove that this efficiency gain is realizable, using a heat storage system consisting of an eight-liter packed bed of aluminum-encapsulated zeolite pellets. Adler lists the advantages: “The packed bed is heated to an even temperature more rapidly. It takes significantly less time to load and unload the heat storage medium. This makes it possible to enhance the efficiency of chemical reactions and hence increase product quality.” The researchers expect that it will be possible to obtain even better results using a metal with a higher thermal conductivity, such as copper. The particles of packing material used in the laboratory tests are five millimeters long and encapsulated in a layer of aluminum with a thickness of 0.25 millimeters. The scientists produce them using a specially developed process that could be easily adapted to mass production. The packing material is poured into long, thin metal tubes, compacted to prevent it from spilling out, and the tubes are then cut into sections to form cylindrical particles no more than a few millimeters in length.
“The chemical industry uses large quantities of packing materials which, ideally, are expected to remain in the reactors for many years. One of the problems is that they are subject to powder abrasion during shipping and when in use, caused by particles rubbing against one another. This no longer happens when they are encapsulated in metal, and so the packing material lasts longer,” says Adler.
Applying heat to zeolite pellets that are saturated with water causes the pellets to dry and absorb heat. When the pellets are rehydrated, the absorbed heat is released. This physical effect makes them suitable for use in heat storage systems. In this application too, says Adler, “the efficiency of the process depends on the thermal conductivity of the zeolite material. It is often necessary to install very complicated heat-exchanger units, which are expensive and reduce the volume available for actual heat storage. The metal-encapsulated packing material could be a valuable improvement here. In the laboratory, we have been able to significantly shorten the heat storage cycle time.”
Now that the researchers have demonstrated the feasibility and functionality of the encapsulation technique in the lab, they want to move on to the next step on the way to industrial application. “We need to further optimize the material and the manufacturing process, and gather data so as to determine exactly to what extent the advantages of higher thermal conductivity outweigh the additional costs of metal encapsulation,” says Adler.
The chemical industry uses large quantities of packing materials as catalytic support media and adsorbents. A catalyst is a substance that accelerates a chemical reaction without undergoing any chemical change itself. An adsorbent removes and stores specific products of a chemical reaction. As well as being used to optimize chemical reactions, packing materials also play a role in modern heat storage systems. In a packed bed reactor, a gas or liquid flows through the material and triggers a chemical reaction on the surface of the tiny particles.
Most read news
Organizations
Other news from the department science
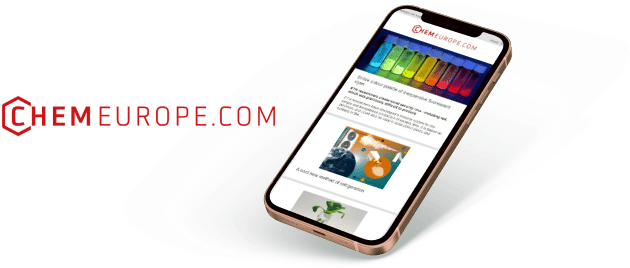
Get the chemical industry in your inbox
By submitting this form you agree that LUMITOS AG will send you the newsletter(s) selected above by email. Your data will not be passed on to third parties. Your data will be stored and processed in accordance with our data protection regulations. LUMITOS may contact you by email for the purpose of advertising or market and opinion surveys. You can revoke your consent at any time without giving reasons to LUMITOS AG, Ernst-Augustin-Str. 2, 12489 Berlin, Germany or by e-mail at revoke@lumitos.com with effect for the future. In addition, each email contains a link to unsubscribe from the corresponding newsletter.