Laser-induced graphene made from wood
Advertisement
Rice University scientists have made wood into an electrical conductor by turning its surface into graphene.
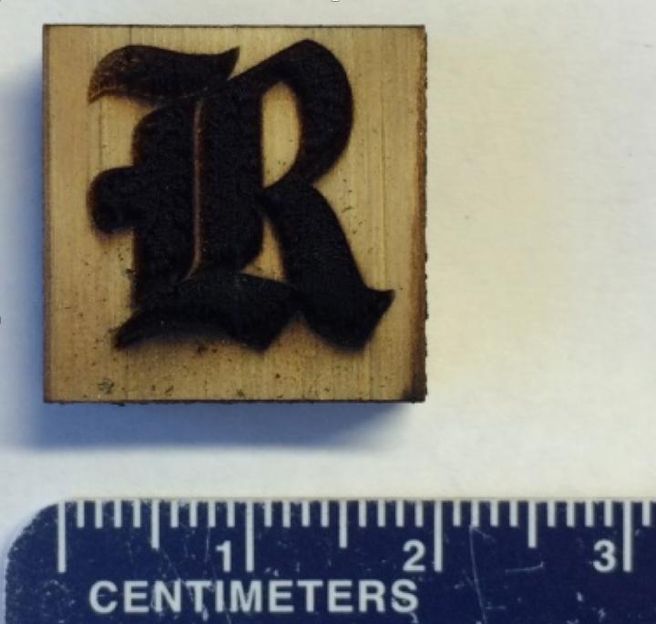
This Rice University athletics logo is made of laser-induced graphene on a block of pine. Rice scientists used an industrial laser to heat the wood and turned its surface into highly conductive graphene. The material could be used for biodegradable electronics.
Tour Group/Rice University
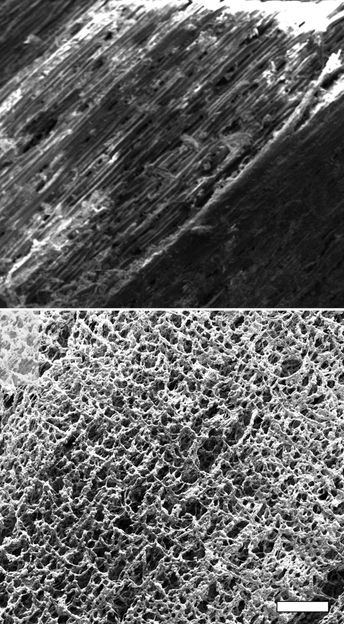
Scanning electron microscope images show pristine pine at top and laser-induced graphene on pine (P-LIG) produced at Rice University at bottom. The scale bar is about 500 micrometers.
Tour Group/Rice University
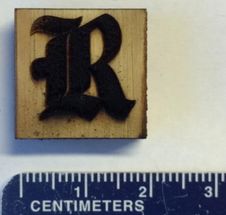
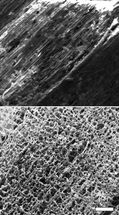
Rice chemist James Tour and his colleagues used a laser to blacken a thin film pattern onto a block of pine. The pattern is laser-induced graphene (LIG), a form of the atom-thin carbon material discovered at Rice in 2014.
"It's a union of the archaic with the newest nanomaterial into a single composite structure," Tour said.
Previous iterations of LIG were made by heating the surface of a sheet of polyimide, an inexpensive plastic, with a laser. Rather than a flat sheet of hexagonal carbon atoms, LIG is a foam of graphene sheets with one edge attached to the underlying surface and chemically active edges exposed to the air.
Not just any polyimide would produce LIG, and some woods are preferred over others, Tour said. The research team led by Rice graduate students Ruquan Ye and Yieu Chyan tried birch and oak, but found that pine's cross-linked lignocellulose structure made it better for the production of high-quality graphene than woods with a lower lignin content. Lignin is the complex organic polymer that forms rigid cell walls in wood.
Ye said turning wood into graphene opens new avenues for the synthesis of LIG from nonpolyimide materials. "For some applications, such as three-dimensional graphene printing, polyimide may not be an ideal substrate," he said. "In addition, wood is abundant and renewable."
As with polyimide, the process takes place with a standard industrial laser at room temperature and pressure and in an inert argon or hydrogen atmosphere. Without oxygen, heat from the laser doesn't burn the pine but transforms the surface into wrinkled flakes of graphene foam bound to the wood surface. Changing the laser power also changed the chemical composition and thermal stability of the resulting LIG. At 70 percent power, the laser produced the highest quality of what they dubbed "P-LIG," where the P stands for "pine."
The lab took its discovery a step further by turning P-LIG into electrodes for splitting water into hydrogen and oxygen and supercapacitors for energy storage. For the former, they deposited layers of cobalt and phosphorus or nickel and iron onto P-LIG to make a pair of electrocatalysts with high surface areas that proved to be durable and effective.
Depositing polyaniline onto P-LIG turned it into an energy-storing supercapacitor that had usable performance metrics, Tour said.
"There are more applications to explore," Ye said. "For example, we could use P-LIG in the integration of solar energy for photosynthesis. We believe this discovery will inspire scientists to think about how we could engineer the natural resources that surround us into better-functioning materials."
Tour saw a more immediate environmental benefit from biodegradable electronics.
"Graphene is a thin sheet of a naturally occurring mineral, graphite, so we would be sending it back to the ground from which it came along with the wood platform instead of to a landfill full of electronics parts."