new "GMP KiloLab" in Bayer's Central Organics Pilot Plant
Providing kilogram quantities of pharmaceutical active ingredients - for phases 1 and 2 of clinical testing, for example - within a minimum of time and with the utmost reliability and safety is a major challenge for every custom manufacturer. Bayer Chemicals, a division of Bayer AG, has a convincing answer to such a challenge: the ZeTOTM GMP KiloLab. Dr. Norbert Lui, plant manager of the ZeTOTM (Central organics Pilot Plant), explains some of its special aspects: "We have a small, experienced and largely autonomous team here, which means we can respond to customers' wishes quickly and flexibly. On the other hand we are part of a major, highly efficient organization, with all the benefits that this brings. We also have state-of-the-art equipment. Added up, it puts us in an ideal position to comply with all our customers' wishes and requirements." Lui was therefore not surprised that, even before the official start of the GMP KiloLab in November 2002, the first external orders were already on the table.
The GMP KiloLab has two main functions, explains Marcus Bock, project manager of the ZeTOTM GMP KiloLab: "First of all, we offer custom manufacturing in the narrower sense, in other words we provide kilogram quantities of APIs (Active Pharmaceutical Ingredients) and active ingredient intermediates. Secondly, we are involved in scale-ups from the laboratory and in process development. In both cases, speed is a major factor for success. "Time is money" is truer here than in most other segments."
The GMP KiloLab - which occupies a useful area of around 200 m2 - has a total reactor volume of some 350 liters. The reactors are made of alloy 59 or steel-enamel. They are equipped for batch sizes of up to about 25 kilograms, and as many as 100 such batches can be dealt with in a year. For the processing, isolation, drying and homogenizing processes, the KiloLab uses suction filters, stainless steel dryers and screening machines. There is also a clean room available (class 100,000) for all product handling. The ZeTOTM GMP KiloLab is qualified according to current cGMP guidelines.
The numerous pieces of apparatus and equipment in the GMP KiloLab are modular in design - for example, the reactor temperature control system, which allows effective control of the reaction between -100 and +220 °C with just two systems. Low temperatures down to -100 °C - which are required in particular in asymmetrical synthesis and with many catalytic reactions - are achieved with the aid of a liquid nitrogen system.
With its expertise in the processing of small and ultra-small quantities, the GMP KiloLab in the Leverkusen Central Organics Pilot Plant is an important cornerstone of Bayer Chemicals' comprehensive custom manufacturing concept. Its range of services is complemented, for example, by Bayer's Laboratory SMB unit, in which - also on a kilogram scale - pure enantiomer active ingredients can be produced from racemates.
Other news from the department research and development
These products might interest you
Most read news
More news from our other portals
See the theme worlds for related content
Topic world Synthesis
Chemical synthesis is at the heart of modern chemistry and enables the targeted production of molecules with specific properties. By combining starting materials in defined reaction conditions, chemists can create a wide range of compounds, from simple molecules to complex active ingredients.
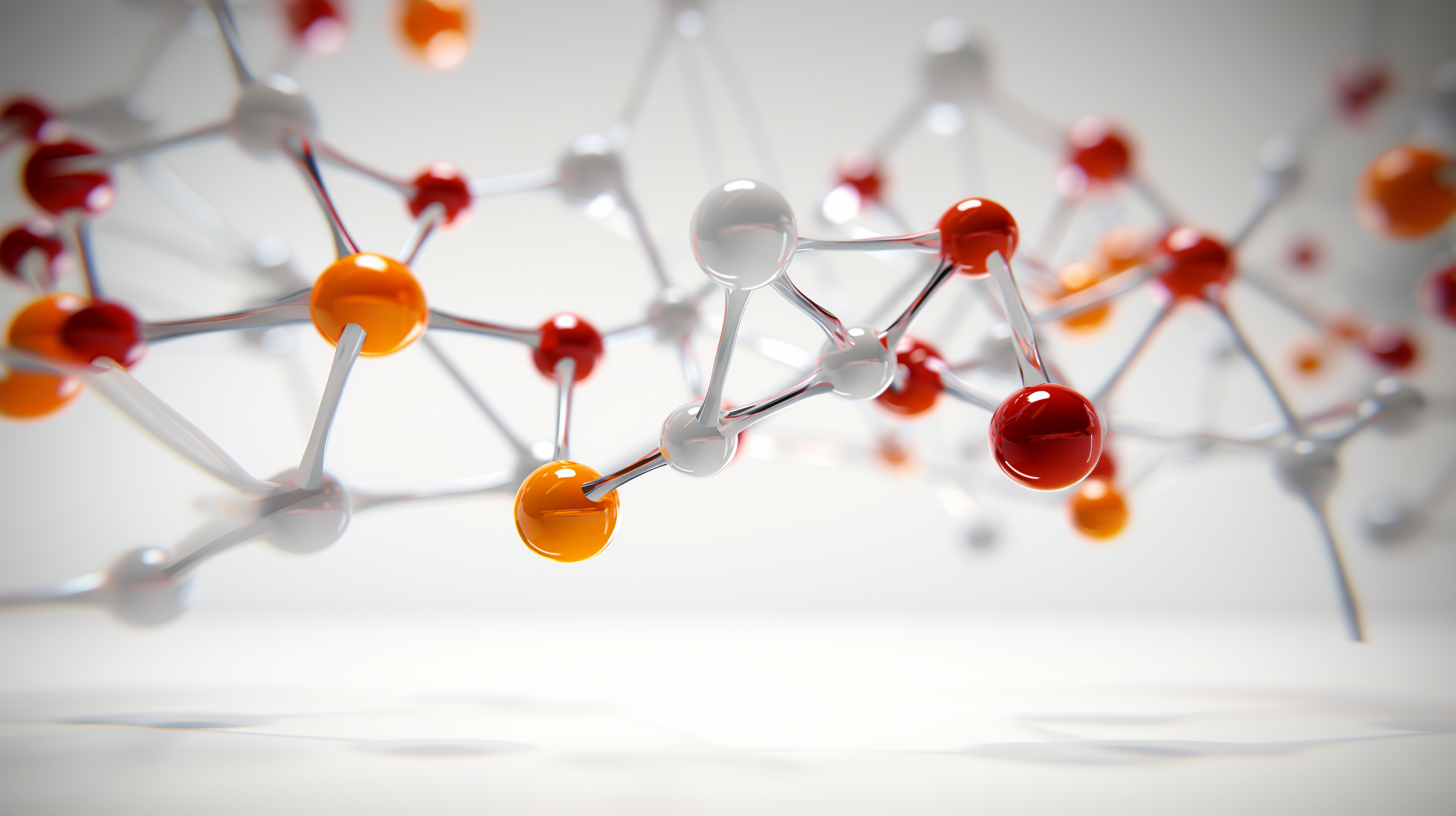
Topic world Synthesis
Chemical synthesis is at the heart of modern chemistry and enables the targeted production of molecules with specific properties. By combining starting materials in defined reaction conditions, chemists can create a wide range of compounds, from simple molecules to complex active ingredients.