BASF with new center of competence for UV curing coatings
BASF coatings AG has combined and significantly expanded its activities in UV curing coatings by putting up a center of competence at its Münster site. Before, these activities had taken place at different sites across the world. The heart of the research and development center consists of a new pilot plant in which the existing experience, gained from coating flat surfaces, is used on the coating of complex three-dimensional parts and large components which may measure up to 150 times 150 centimeters. BASF invested a total of 1.2 million euros in this pilot plant.
"We want to consistently research and advance all aspects of radiation-curable coatings," is the explanation that Klaus Peter Löbbe, President of the BASF Group's Coatings Division and CEO of BASF Coatings AG, gives for the building of the competence center. The most important objective is definitely the further development of these innovative coatings for their use in the automotive industry. In the wood, foil and plastics coatings sectors, UV processes have already been largely established. As all these materials are heat-sensitive, UV curing with its low thermal stress is in many cases the best suited solution.
Eco-efficient UV coatings gain importance
Coatings being cured and crosslinked by means of UV radiation are gaining more and more importance due to their eco-efficient properties. On the one hand, they are very easy on the environment as they are usually solvent-free and thus comply with the increasingly stricter regulations that were imposed to limit the emission of volatile organic compounds (VOC). On the other hand, they allow a high process speed, which is required for many industrial manufacturing processes, because the coated parts are immediately ready for further processing, packaging or stacking after their exposure to radiation. A high quality surface with good mechanical properties, chemical resistance and high gloss is achieved. And the economic advantages also play an important role, e.g. space-saving equipment, low costs, low energy consumption and low thermal stress especially to heat-sensitive materials that need to be coated. These positive conditions let the market for radiation-curable coatings grow by six percent annually. The European market has reached a volume of almost 72,000 tons representing a value of about 600 million euros.
A scratch-resistant skin for cars
A pro for the introduction of similar processes in vehicle manufacturing is the range of properties which is brought forth by UV systems, namely a combination of high chemical resistance and a significantly improved scratch-resistance. With regard to these two properties in particular, the "automotive skin" is still capable of improvement. "The UV-coating of lenses and vehicle head lights made of polycarbonate plastics has shown that the scratch-resistance can be improved significantly," says Dr. Uwe Meisenburg, scientific head of the UV competence center in Münster. It is necessary to solve two problems when applying the system in the automotive industry: First, the compatibility of the UV clear with the basecoat must be ensured and second, the UV light must also reach the so-called "shadowy zones" of the three-dimensional car body.
Most read news
Other news from the department science
These products might interest you
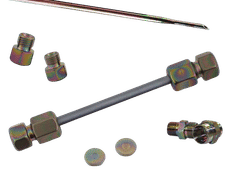
Dursan by SilcoTek
Innovative coating revolutionizes LC analysis
Stainless steel components with the performance of PEEK - inert, robust and cost-effective
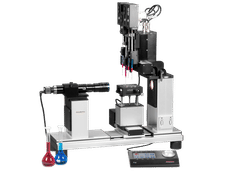
OCA 200 by DataPhysics
Using contact angle meter to comprehensively characterise wetting behaviour, solids, and liquids
With its intuitive software and as a modular system, the OCA 200 answers to all customers’ needs
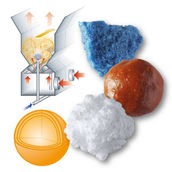
Tailor-made products for specific applications by IPC Process Center
Granulates and pellets - we develop and manufacture the perfect solution for you
Agglomeration of powders, pelletising of powders and fluids, coating with melts and polymers
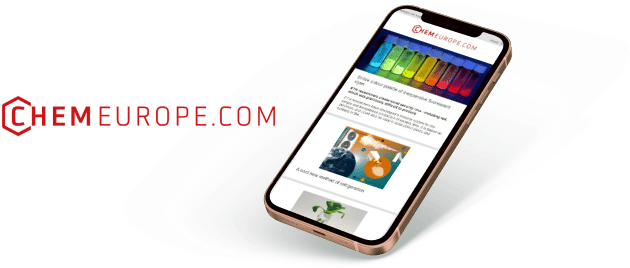
Get the chemical industry in your inbox
By submitting this form you agree that LUMITOS AG will send you the newsletter(s) selected above by email. Your data will not be passed on to third parties. Your data will be stored and processed in accordance with our data protection regulations. LUMITOS may contact you by email for the purpose of advertising or market and opinion surveys. You can revoke your consent at any time without giving reasons to LUMITOS AG, Ernst-Augustin-Str. 2, 12489 Berlin, Germany or by e-mail at revoke@lumitos.com with effect for the future. In addition, each email contains a link to unsubscribe from the corresponding newsletter.
Most read news
More news from our other portals
Last viewed contents
Polycarbonate
Lactobacillus_brevis
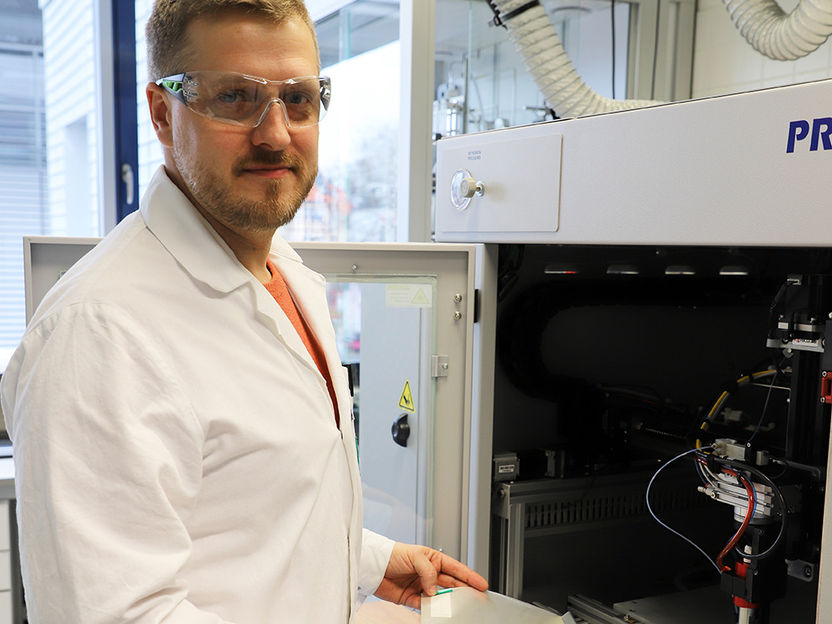