A quieter, safer world is taking shape thanks to developments in adaptronic materials
The thin, slightly bent metallic thread lding looks like a piece of ordinary florist's wire. But you only have to touch it to realize that this wire is made of a very special material. The metal feels soft and warm, like a blend between a fishing line and a copper wire. Kautz holds the thread over a flame. Within seconds, the bent wire curls itself into a perfect paper clip.
Kautz, a specialist in memory metals at Siemens Corporate Technology (CT) in Erlangen, Germany, is working on materials that can "remember" the shape into which they were originally formed. These substances are evolving into a promising production material that could open a new field known as adaptronics-the marriage of "adaptation" and "electronics."
Adaptronics engineers are after something new. They want to develop materials or components that are so smart they can automatically adapt to their surroundings. Under ideal circumstances, these materials combine sensors, regulators and actuators in a highly compact space.
According to experts such as Siemens' Kautz, such materials are multifunctional. That is, they can register alterations in their surroundings-for example, changes of temperature-and respond immediately. The first prototype components of this sort have already been produced. "Memory metals are excellent examples of adaptronics," says Kautz, who explains that If they are heated or subjected to a voltage, they change shape. They do this by means of a simple, temperature-dependent alteration of their atomic lattice structure-no complex electronic manipulation is required.
Memory Metal in the Dishwasher. Only recently, a memory metal actuator-a wire made of nitinol (a nickel-titanium alloy)-produced in Kautz's laboratory went into production. The wire is part of an optical sensor in the latest range of dishwashers produced by Bosch and Siemens. This "optosensor" measures the calcium content of the water up to ten times during the dishwashing program and uses this data to regulate the release of a special salt. The memory wire, which is activated by a small jolt of electric current, is designed to open a small valve that expels water from the sensor. In the process, the wire, which is 10 cm long, contracts by 5 mm and develops astonishing strength in spite of being just 0.25 mm thick. "Because the wire automatically reacts to voltage changes, complicated control technology is unnecessary," says Kautz. All in all, the optosensor and its entire mechanism is no larger than the smallest pocket calculator.
Meanwhile, Siemens CT researchers are working on integrating a sensor, an actuator and a regulator into a single tiny component. "That would open up a new range of potential applications," says Holger Hanselka, director of the Fraunhofer Institute for Structural Durability (LBF) in Darmstadt, Germany. Hanselka, who works at the University of Darmstadt, is one of a handful of people around the world who teaches adaptronics. "These compact and lightweight adaptive materials are ideally suited for integration into lightweight production materials," he says. According to Hanselka, lightweight materials are the wave of the future in fields such as automobile and airplane production. However, due to their low mass, such materials tend to vibrate, thus generating noise and other problems. Adaptive materials can help here, as they can register when a material starts to vibrate. The sensor's signal is processed by a regulator, which then causes an actuator to dampen the vibrations through countermovements.
Researchers at the Fraunhofer Institute have succeeded in spinning ceramic piezofibers into long, thin threads that are ideal for adaptronic materials In view of this, Hanselka and others are placing high hopes in a new generation of piezomaterials, which are true masters of versatility. The materials can transform electrical energy into mechanical energy and vice versa. Some cigarette lighters, for example, generate the energy that sparks the flame from a piezocrystal that is put under mechanical pressure. A joint project carried out by a number of Fraunhofer Institutes has succeeded in spinning piezomaterials into long fibers that are only 20 to 30 µm in diameter. In this process, the fibers are produced using the so-called sol-gel process. The "sol" is a solution of molecules that is pressed through tiny nozzles and at the same time hardened into a gel by means of chemical reactions or changes in temperature. This creates long threads which then gently coagulate into crystalline piezofibers without breaking. "These fibers are so fine that they can be easily integrated in lightweight composite materials," says Dr. Dieter Sporn of the Fraunhofer Institute for Silicate Research (ISC) in Würzburg, Germany, which played a key role in the development of this process. "In the past, piezo components were generally so big that they interfered with the structure of lightweight materials."
Both the new fibers and the piezo foils that have long been in use can simultaneously fulfill the functions of a sensor and an actuator. For example, if a piezomaterial is activated by undesirable vibrations, it generates an electrical signal that can be interpreted by a controller. The controller, in turn, transmits an electrical pulse back to the fiber, which then bends in a particular direction. The fiber generates a kind of counter-pull that blocks the vibration in its early stages. Combined with the appropriate software, this kind of closed-loop control can cushion even large components.
Piezofibers and Quiet Cars.^ To find out what kinds of future developments may be possible in adaptronics, scientists representing over 20 companies and research institutes have been involved in the "Adaptronics Pilot Project." The goal of this initiative, which was supported by the German Ministry of Research and concluded in late 2002, was to develop components that could be used to create adaptronic products. One of the products developed in the project was an adaptive car roof made of lightweight materials that could effectively dampen vibrations using piezofoils and piezofibers. According to Hanselka, this technology is ready for the next generation of vehicles. He expects, however, that this kind of car roof will initially be installed only in a small number of premium-segment vehicles.
Dieter Sporn believes that the fibers also have a future in the aerospace industry. For example, the rudder units of today's Airbus jets consist of composite materials. Inspection of these units for hairline cracks and hidden damage is a time-consuming process, as the rudder unit must be scrutinized with ultrasound. Adaptive materials would make this process unnecessary. "A mesh of piezofibers integrated into the material could detect cracks that subject the fibers to mechanical tension and directly transmit this information to analytical software," says Sporn, adding that piezofibers could significantly simplify safety checks.
Adaptive piezotechnology can also help to make driving safer. Prof. Hans Meixner, head of the Sensor and Actuator Systems Competence Center at Siemens Corporate Technology Center in Munich, is developing a new automotive sensor designed to ensure that tomorrow's airbags inflate correctly. To this end, stretch measurement strips made of piezofibers will be integrated into vehicle seats. As the degree of stretching depends on the occupants' weight, passengers will be better protected in the event of a crash. At present, airbags inflate with the same degree of force, regardless of whether a small child or a heavy adult is sitting in the seat. Thanks to the information provided by stretch measurement strips, future airbags will inflate with an intensity that will softly cushion each passenger.
Quieter MR Scanners. Another promising application area is medical electronics. For instance, Dr. Hans-Georg von Garßen and his colleagues at CT in Munich and Erlangen are working on piezofibers that can dampen vibrations in magnetic resonance (MR) tomographs. Because the magnetic field generated by these machines must constantly change its direction as it moves along a patient's body, forces are generated that cause the funnel of the patient entry tube to vibrate. At 120 db, the resulting noise can be as loud as a jet plane taking off. The worst problems are caused by low frequencies, which disturb not only the patient inside the MR machine, but also medical personnel. Garßen and his team hope to dampen these vibrations by using numerous strips of piezofoil the size of small bandages. When glued to the funnel, the strips of fiber act as sensors and actuators simultaneously. The challenge is to determine exactly how the funnel is vibrating at a given time, and how the vibration dampers can be precisely
Other news from the department science
These products might interest you
Most read news
More news from our other portals
See the theme worlds for related content
Topic world Sensor technology
Sensor technology has revolutionized the chemical industry by providing accurate, timely and reliable data across a wide range of processes. From monitoring critical parameters in production lines to early detection of potential malfunctions or hazards, sensors are the silent sentinels that ensure quality, efficiency and safety.
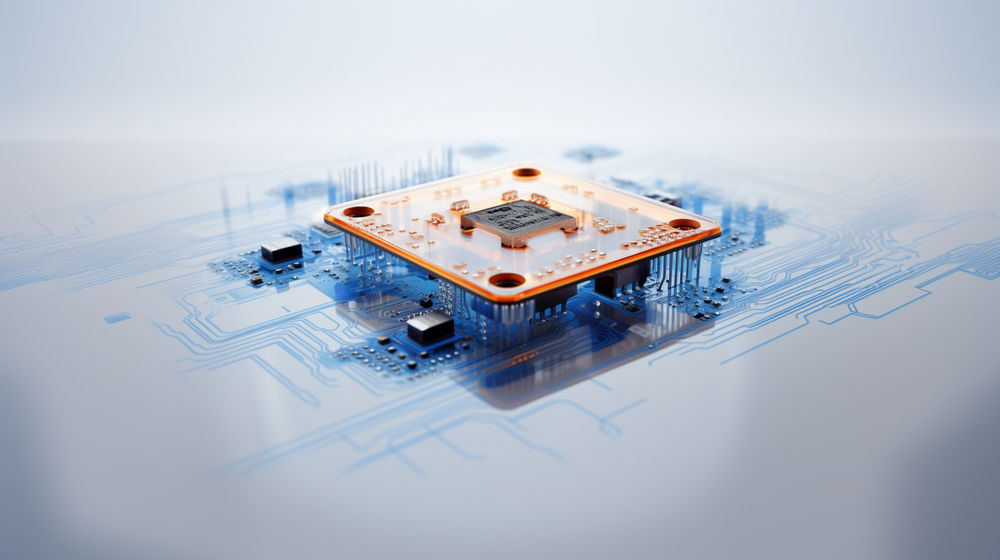
Topic world Sensor technology
Sensor technology has revolutionized the chemical industry by providing accurate, timely and reliable data across a wide range of processes. From monitoring critical parameters in production lines to early detection of potential malfunctions or hazards, sensors are the silent sentinels that ensure quality, efficiency and safety.